ADVANCED ARC WELDING PROCESSES FOR
FABRICATION OF STRUCTURES
A.Raja and R.Easwaran
Welding Research Institute,Bharat Heavy Electricals Limited, Tiruchirappalli-620014
1. Introduction
The global industrial competition demands increased productivity, better quality and reduced cycle time in manufacturing operations. This is in line with the present trend in industries of higher output and increasing large-scale production. Increasing demand for higher productivity and quality in welding has been addressed by the development of advanced variants on existing arc welding processes. Several advanced arc-welding process variants have been developed in the recent times to achieve improved quality and productivity. These new variants are mostly developed around Gas Metal Arc Welding (GMAW) and Submerged Arc Welding (SAW) processes. The following are some of the advanced variants developed around GMAW process as the basis.
[Examples: Fronius TIME Twin, Cloos Tandem GMAW, Lincoln Tandem MIG etc.],
- Deep penetration mode GMA welding
[Examples: EWM Forced Arc, Lincoln Rapid Arc etc.],
- Waveform controlled short circuiting transfer GMA welding
[Examples: Lincoln STT (Surface Tension Transfer), Miller RMD (Regulated Metal Deposition), Kemppi Fast-MIG, Fronius CMT (Cold Metal Transfer) etc.]
Some of the advanced variants developed around SAW process are:
-
Waveform controlled SAW
- Tandem SAW / multi-wire SAW
Development of these advanced processes is made possible by the advancements in electronics, computer technology and modern welding power source design. Most of the advanced arc welding processes are intended for use in mechanized welding mode employing robot or SPMs as manual handling of these processes is difficult due to high amperages and welding speeds involved. This paper discusses the operating principle of some of these advanced arc welding processes, their applications and advantages in fabrication of structures.
2. Variants of GMAW
Gas Metal Arc Welding [GMAW] traditionally operates with a single wire connected to a constant voltage power source and argon/CO2 shielding gas to protect the weld puddle from atmospheric contamination. With single wire, the wire feed rate can go up to 18 m/min. Stretching the wire feed rate beyond 20 m/min results in unstable arc and welds with severe undercut. Tandem GMAW [example – Fronius TIME Twin, Lincoln Tandem MIG etc.] with two wires operating on a common weld puddle and common shielding gas has been developed to increase deposition rate and welding speed much beyond the range possible with single wire GMAW. Deep penetration mode of GMA welding [EWM Force Arc, Lincoln Rapid Arc etc.,] has been developed to achieve higher penetration in fillet, groove welding of structures. Waveform controlled Short circuiting transfer [example: Lincoln-STT, Miller-RMD, Kemppi-Fast-MIG mode etc.] mode of welding has been developed to avoid spatter lack-of-fusion problem in short circuit transfer welding through close looped waveform control of the process.
2.1. Tandem GMAW
In conventional GMAW process with a single wire, deposition rate of up to 6 kg/hr can be obtained. In Tandem GMA welding such as TIME Twin, where two wires are used simultaneously the deposition rate can be increased by more than two times. The Tandem GMAW extends the welding productivity range beyond that possible with conventional single-wire processes. In tandem GMAW [Fig. 1] process two electrode wires are fed into a common weld-pool, but through two separate and electrically isolated contact tubes. The two independent arcs from the two wires are protected from the atmosphere by a common shielding gas supplied through the nozzle. Besides, both arcs are acting on a common weld-pool [Fig. 2]. The Tandem GMAW process gives higher deposition rate. The higher deposition rate can be advantageously converted into higher welding speed or higher cross section of the weld seam depending on the requirement.
In conventional GMA welding, there is only limited scope for high arc power to be translated into higher welding speeds. This is because when the arc power is increased; the arc pressure rises rapidly, making the weld pool difficult to control. For instance, with a 1.2 mm diameter AlMg wire electrode, the amperage limit beyond which weld-pool control becomes critical will be found between approximately 320 and 350 A at a wire feed speed of 20 to 22 m/min [1]. The Tandem GMAW with two wires and separately controllable metal transfers enable welding at higher amperages and thus higher welding speeds. As a rule, a slightly higher power is set for the leading arc. The cold base metal is thus thoroughly melted and exact fusion takes place into the root. The weld-metal deposit from the second electrode fills the weld pool. Also, the trailing arc prolongs the weld-pool degasification time, lessening the pore-formation sensitivity.
This Tandem GMAW process finds application in automobile manufacturing, shipbuilding, boiler manufacturing, construction and other areas. In the automobile sector, Tandem GMAW is employed for welding of truck wheel made of steel. In this application, Tandem GMAW provides higher welding speed; low spatter, good fusion and fine weld shape.
2.2. Deep Penetration GMA Welding:
In the recent past, the deep penetration mode in GMAW has been identified and the operating zone of this deep penetration mode is found to lie [Fig. 3] just below the parametric window for spray transfer. It is a forced short circuiting transfer mode of welding that operates at voltages little less than spray but wire feed speeds exceeding those of spray arc welding. It is characterized by a shorter arc with more plasma pressure and as such it is a mixture between short circuiting transfer and spray transfer modes. The deep penetration is called by different trade names such as Force Arc, Rapid Arc etc.
The deep penetration arc mode operates at wire feed speeds from 10 to 20 m/min. The higher wire feed speed forces a depression into the molten weld puddle and creates a buried arc condition, which increases side wall and root penetration. Higher travel speed is also obtained, which reduces heat input. Weld spatter is reduced by short arc length, which provides higher energy density metal transfer and produces finer weld spatter that generally does not adhere to the base metal.
The relatively low arc voltage employed in deep penetration technique permits a faster welding speed without undercut. At the same time, high weld reinforcement is limited by a certain combination of the welding parameters and forehand welding technique. Argon based (92%Ar+18%CO2) shielding gas is used with a higher flow rate than normal. The welding current and electrode extension is much higher than for normal short arc welding. The process was developed for welding of smaller weld sizes and thin sheets at higher travel speeds. Deposition rates of 10 to 15 kg/hr can be achieved. Higher welding speeds, lower spatter, good surface quality, excellent penetration, low heat input and less distortion are the advantages of this process.
Equipment manufacturers have perfected this deep penetration GMA welding by developing electronic power sources with excellent dynamic control aimed at stable arc and minimized spatter. The deep penetration GMA welding is now available as a promising feature in the modern GMAW power sources under proprietary names such as Force Arc [EWM], Deep Penetration MIG [Kemppi] etc. It provides adequate root penetration in critical applications ensuring sound weld quality. These modern inverter power sources with good dynamic regulation offers directionally stable arc and minimized spatter.
2.3. Waveform Controlled Short Circuiting Transfer GMA Welding:
The conventional short circuit transfer or dip transfer is associated with spatter and lack-of-fusion defects. Waveform controlled short circuit transfer GMA welding technique has been developed to overcome the above deficiencies of conventional short circuit or dip transfer GMA welding. In the newer technique, at the onset of short circuit (detected by the voltage waveform minimum) the current rise is delayed [approximately 0.5 m.sec for argon rich shielding gases and 1.5 m.sec for CO2] to allow adequate wetting in of the droplet into the weld puddle. Prior to the rupture of the short circuit the current is reduced to a low level and the transfer of the droplet continues under the influence of surface tension without the disruptive influence of high electromagnetic forces. The result is virtually a spatter free dip transfer, stable over a wide range of current even under CO2 shielding gas. There are now around 10 variants of the waveform controlled dip transfer GMAW process viz., STT, CMT, Fast Root etc. commercially available [2].
In the advanced technique, the wire feed speed and current is controlled independently. Unlike conventional GMAW, which employs a constant voltage power source with DC continuous current, the advanced dip transfer technique like STT employs wave form control technology to precisely control current [Fig 4] and thereby regulate the physical processes involved in short circuit transfer welding [3]. The power source employed, for instance, in STT process operates neither in the constant current nor constant voltage mode. Rather, it is a current controlled machine wherein the power to the arc is based on the instantaneous arc requirements, not on an "average DC voltage." The welding current supplied by the power source is guided by the state of the arc voltage. The effectiveness of this process in controlling spatter and lack-of-fusion problems lies in this particular capability of the power source.
Optimum arc characteristics are maintained even with variation in stand-off distance thus releasing the welder from the need to maintain exact lengths and welding gun angles in order to produce smooth, low spatter, high integrity weld. The waveform controlled dip transfer process is widely used in fabrication of tubular structures to achieve enhanced weld quality and greater productivity. The plasma boost causes the arc to broaden: melting a wider surface area; avoiding lack-of-fusion problem. As a result the waveform controlled dip transfer process is widely used in fabrication of tubular structures to achieve enhanced weld quality and greater productivity.
3. Variants of Saw
Submerged Arc Welding (SAW) is used in the pipe manufacturing, windmill construction, in pressure vessel construction and in shipbuilding. SAW is nearly a fully automated process with higher deposition rate and welding speed compared to other arc welding processes. Waveform controlled SAW and tandem / multi-wire SAW are built around basic SAW process to further enhance the deposition rate and thereby the productivity.
3.1 Waveform Controlled SAW:
Digital square wave alternating current (AC) power sources with variable balance control (i.e. independent control of the positive and negative polarity dwell times in the AC welding cycle) have been developed for SAW. The positive polarity of the welding cycle provides more heat to the work piece to promote enhanced melting of the base metal for improved fusion and penetration, whereas the negative polarity provides more heat at the electrode tip for enhanced melting of the continuously fed electrode for improved weld deposition rates. A conventional AC welding sine wave provides a 50/50 balance of negative and positive polarity, and therefore a balance between fusion/penetration and electrode melt off rates. However, with variable balance (also known as variable polarity) waveform technology, the melt-off rate and thus weld deposition rate can be optimized by increasing the amount of negative polarity dwell time in the AC welding cycle. Increasing negative polarity dwell time results in reduced positive polarity dwell times and therefore reduces the amount of heat into the work piece, thus promoting higher weld zone cooling rates (for improved impact toughness due to smaller CG-HAZ grain size) and reduced shrinkage stresses for less angular distortion. Conversely, increasing negative polarity dwell time results in higher electrode melt-off and thus improved weld deposition and productivity. Furthermore, the square wave form characteristic has been shown to result in a much more stable arc compared to a conventional AC sine wave, leading to fewer weld defects.
3.2 Tandem/Multi-wire SAW
Tandem SAW uses two separate power supplies, two wire feeders and two large diameter wires typically 4.0 mm. Both wires feed into same molten puddle, but each has separate contact tip, power supply and control. Deposition rates are at least double as that of single wire SAW. The lead arc is most often DC (+) and the trail arc will be AC. The DC (+) arc provides deep penetration and while the AC trail wire fills the weld joint at a higher deposition rate [4]. The important aspect of the AC trail arc is that it does not cause significant interference with the lead arc.
Modified waveform tandem SAW welding is a process that uses AC square wave power source for trailing arc, so that its timing and amplitude are unbalanced. The imbalance is biased toward negative polarity as this provides higher deposition rate.
Multi wire SAW significantly enhances the deposition rate and welding speed with 3 or 4 being usual number of wires. However, up to six wires can be used together, each with their own power source. The lead wire is usually DC+ polarity with the trailing wires being AC. Welding speeds of up to 2.5 m/min can be achieved giving a maximum deposition rate of 90 kg/hr. This technique is particularly suitable for longitudinal pipe welding.
4. Concluding Remarks
The modern variants of GMAW process namely Tandem GMAW, Deep penetration mode of GMA welding, Waveform controlled Short circuiting transfer mode of welding and SAW process namely waveform controlled SAW, multiple wire SAW etc. with their advanced features are capable of providing improved weld quality and productivity in the fabrication of structures.
References
- Karin Himmelbauer: TIME Twin digital – Top deposition rate thanks to two wire electrodes, Fronius, Austria. url: http://www.fronius.com/cps/rde/xbcr/SID-6BF54F8D-34579AB4/fronius_usa/21_timetwin_digital_gb.pdf
- John Norrish: Process modification in gas metal arc welding for enhanced performance. Australian Welding Journal, Vol58, First Quarter, 2013.
- Bruce D. DeRuntz: Assessing the benefits of Surface Tension Transfer Welding to Industry. Journal of Industrial Technology, Vol.19, No.4, 2003.
- Improving productivity with submerged arc welding. May 25 2010. The Fabricator.com.
Acknowledgement:
The authors sincerely thank the management of M/s Bharat Heavy Electrical Limited, Trichy for kindly according permission to present the paper in the Steelcon seminar held on 26-27th April 2013 at Mysore.
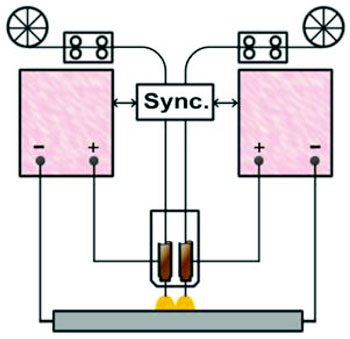 |
Schematic of Tandem GMAW process |
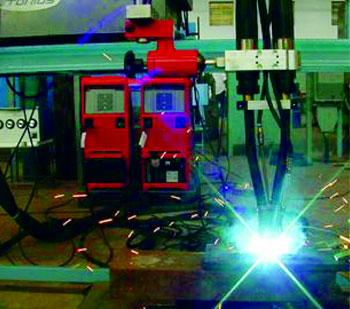 |
Tandem GMAW in operation |
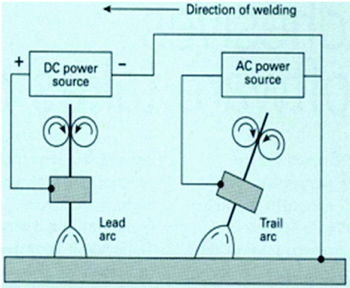 |
Schematic of Tandem Submerged Arc Welding |