High Performance Cellular Concrete
There are two ways to produce light weight concrete. One way is to use naturally available lightweight rock aggregates such as pumice [most widely used], scoria, volcanic cinders, tuff and diatomite or artificial rotary kiln produced lightweight aggregates such as expanded clays, slates, slag, Perlite or shale’s. Cenospheres [hollow sphere comprised largely of silica and alumina with cavities filled of inert gases such as nitrogen and carbon dioxide] and recycled glass beads are additional multi-functional fillers. These low-density aggregates may function well; however they are economically available only in the vicinity of blast furnaces and are becoming increasingly expensive with increased material, fuel and labor costs.
Figure 1: Schematic representation of Foam Concrete Production
The other way is by introducing a relatively large amount of air that can be entrained in the concrete without substantially reducing the strength of the ultimate structure. This can be done by using a new, improved mechanical air-entraining admixture or concrete containing air cells or voids throughout its volume. Such a concrete is called- SDC: Specified Density Concrete or HPCC: High-Performance Cellular Concrete.
Figure 2: Schematic Representation of AAC Concrete Product
Cellular Concrete
Cellular Concrete is a cementitious paste of neat cement or cement and fine sand with a multitude of micro/macroscopic discrete air cells uniformly distributed throughout the mixture to create a lightweight concrete.
It is commonly manufactured by two different methods.
- First method consists of mixing a pre-formed foam [surfactant] or mix-foaming agents mixture into the cement and water slurry. As the concrete hardens, the bubbles disintegrate leaving air voids of similar sizes. A foam concentrate consisting of a stabilizer, solvent, surfactant, water and alkaline polymer mixed in specified order and proportions, is foamed in a foam generator. A predetermined amount of the foamed foam is injected into normal density concrete slurry in a continuous mixer. After sufficient mixing, the foamed, cellular concrete is ready for placement. Foam concrete production is schematically represented in Figure 1.
- Second method, known as Autoclaved Aerated Concrete [AAC] consists of a mix of lime, sand, cement, water and an expansion agent. Figure 2 shows schematic representation of AAC Concrete product. The bubble is made by adding expansion agents [aluminum powder or hydrogen peroxide] to the mix during the mixing process. This creates a chemical reaction that generates gas, either as hydrogen or as oxygen to form a gas-bubble structure within the concrete. The material is then formed into molds. Each mold is filled to one-half of its depth with the slurry. The gasification process begins and the mixture expands to fill the mold above the top. Similar to baking a cake. After the initial setting, it is then cured under high-pressured-steam [180° to 210°C / 356°to 410°F] “autoclaved” for a specific amount of time to produce the final micro/macro-structure.
Recently, a direction to concrete compositions prepared by using aqueous gels [aqua gels] is being considered as all or part of the aggregate in a concrete mix. Aqua gel spheres, particles, or pieces are formed from gelatinized starch and added to a matrix. Starch modified or unmodified such as wheat, corn, rice, potato or a combination of a modified or unmodified starches are examples of aqueous gels. A modified starch is a starch that has been modified by hydrolysis. Agar is another material that can create a pore or cell in concrete. During the curing process as an aqua gel loses moisture, it shrinks and eventually dries up to form a dried bead or particle that is a fraction of the size of the original aqua gel in the cell or pore in the concrete. This results in a cellular, lightweight concrete.
High carbon ash, recycled aluminum waste and zeolite powders are additional mechanical structures suitable in the production of cellular lightweight concrete. These cells may account for up to 80% of the total volume. Weight of the concrete mixtures range from 220 kilograms per cubic meter [l4 lbs. cubic foot] to 1922 kilograms per cubic meter [120 lbs. cubic foot] and compressive strengths vary from 0.34 Mega Pascal [50 pounds per square inch] to 20.7 Mega Pascal [3,000 pounds per square inch].
High-Performance Cellular Concrete [HPCC]
LWC-Sustainable masonry smart wall systems
HPCC, the High-Performance Cellular Concrete, has all the properties of cellular concrete and can achieve 55.37 MPa [8,000 psi]. Higher strengths can be produced with the addition of supplementary cementitious materials. Density and strengths can be controlled to meet specific structural and nonstructural design requirements, while in conventional cellular concrete these cannot be achieved.
High-performance concrete is defined as “concrete which meets special performance and uniformity requirements that cannot always be achieved routinely by using only conventional materials and normal mixing, placing and curing practices.” The requirements may involve enhancements of characteristics such as ease of placement and compaction without segregation, long term mechanical properties, density, volume, endurance, stability, or service life in severe or hostile environments.
Density is the best characteristic feature of cellular concrete. While the lowest densities are being used for fills and insulation, the higher densities are being used for structural applications, leading to a substantial reduction in the dead weight of a structure. 0.028 cubic meters [one cubic foot] of foam in a matrix replaces 28.30 kilograms [62.4 lbs.] of water, or 0.028 cubic meters [one solid cubic foot] of aggregate weighing 74.84 kilograms [165 lbs. per cubic foot].
HPCC has an excellent insulation property that significantly reduces the transfer of heat through the concrete member. This bubble is accountable for a superior freezing and thawing resistance and thermal reduce conductivity, low water absorption, high tensile strength, high fire resistance and sound retention, and corrects deficiencies in the sand that causes bleeding. Forming, conveyance, placing and finishing systems for cellular concrete are no different than current methods in the construction industry.
Advantages of Foamed Concrete
- Cost reduction for raw materials- By adding air, the volume of concrete can be increased at very low cost.
- Energy savings/ environmentally-friendly-In contrast to autoclaved aerated concrete (AAC/ gas concrete), air This saves up to 9 m curing is possible for foamed concrete.3 of gas for curing one cubic meter of AAC and therefore protects our environment.
- Weight Reduction- Less steel reinforcements required.
- Cost reduction for transportation and storage-Less raw materials, very efficient.
- Improved thermal insulation-Foam concrete can achieve the same insulation results as normal concrete with only 20% of the weight and 10% of raw materials.
- Improved fire protection
- Easy to use/ produce/ handle
- Low investment-Just one simple machine required.
- High flowing capability-Can fill hollow spaces.
- Low water absorption-Only 10–15%, if specific foaming agents are being used in combination with silicon oil in the cement slurry, the water absorption rate can be decreased to only 1%.
The Process
Fig: Making from Foaming Agent, Water and Compressed Air.
Conventional cellular concrete produced with a pre-formed foam mixture is produced by discharging a stream of preformed foam into a mixing unit on site or a transit mix load of sand-cement grout or cement-water slurry. This foam [surfactant] resembles shaving cream or the foam used for firefighting. Most of the foam concentrates are hydrolyzed proteins or synthetics and are available through proprietary sources. Amine and amine oxides, naphthalene sulphonate formaldehyde condensates are examples of these. Some of these products can contain a substance or substances classified as dangerous or hazardous to the environment, cautious attentiveness should be considered when using these products, especially towards the formaldehyde condensates, butyl carbitol, and glycol ethers.
Expandable Polystyrene Beads
Depending on an application using foam produced from a surfactant usually is not an environmental issue. However in some countries this can be a religious concern/significance. This would be the case when using hydrolyzed protein based surfactants that contain keratin or casein derivatives.
Surfactants are surface-active substance or agent [detergents, wetting agents, emulsifiers] that when added to water lowers surface tension and increases the “wetting” capabilities of the water, thus improving the process of wetting and penetrating that surface or material. When agitated forms a large mass of micro/macroscopic bubbles.
With this device or process [HPCC] a surfactant [wetting agent] or foam concentrate is diluted with water to form a foam solution. This solution is then injected with compressed air through a blending device or foam generator. The quantity of the foam injected into the mixture proportions is in the range of 0.07 to 0.40 per cubic meter [2 to 11 cubic foot per cubic yard] of concrete. The water/cement ratio [w/cm] is in the range from 0.23 to 0.32 and foam of microscopic bubbles with at least a majority being in the range from 25 μm to 100 μm [0.025mm to 0.1 mm / 0.001 inches to 0.004 inches] in diameter. * Normal cellular concrete bubble range is 0.3 mm - 0.8 mm [0.012 in. - 0.032 in.] in diameter.
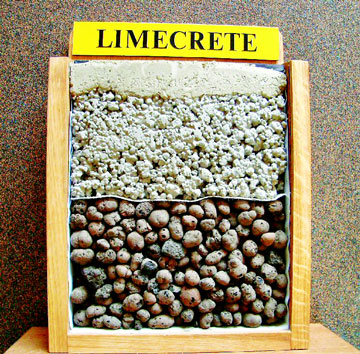 |
Concrete is formed by mixing the liquid cement paste with predetermined qualities of aggregate material. The aggregate is typically made up of medium and coarse aggregate or rock and fine aggregate or sand. Or the next generation of fillers that are artificial or recycled. These to include natural/artificial pozzolans, recycled glass, ceramic, expanded polystyrene beads, plastic, organic or inorganic materials.
In conventional concrete, the percentage of sand in the aggregate is 30% to 40%. However, the foamed cement of this process/invention is preferably mixed with an aggregate having a higher ratio of sand, preferably in the range of 40% to 50%. This reduces or eliminates voids in the concrete mixture, since gaps between larger rock particles may be filled with a combination of smaller rock, sand, and air bubbles. The smaller the spacing factor, the more durable the concrete will be. These microscopic bubbles are smaller than the size of the sand particles increasing the plasticity or flowability of the mix.
As the concrete hardens, the bubbles disintegrate or transform, releasing the water which is absorbed into the cement matrix, thus aiding in the hydration process and leaving air voids of similar sizes. Thus, there is less need to wet the concrete during curing, as is normally necessary with conventional, un-foamed concrete.
An air-entraining admixture must produce stable air bubbles that won’t coalesce to form larger bubbles during mixing. For a given air content or volume of air, if bubbles are too large, there won’t be enough of them present to properly protect the paste. Large bubbles are also more likely to break while the concrete is being mixed, transported, placed and vibrated. If too much air is lost during these operations, the remaining air voids may not adequately protect the hardened concrete during cold weather or thermal conductivity. To prevent air loss, the bubble skin must be stable and tough enough to resist breaking and coalescing, and the size must be extremely small, minute or microscopic.
Segregation
Aggregate gradation significantly affects concrete mixture proportioning and workability. The particle size distribution, particle shape and surface texture are all important elements in the assurance of concrete quality and durability. Variations in grading materials, either by blending selected size aggregates or an adjustment of concrete mix proportions involves constant attention to meet a performance specification.
When particles are poorly distributed within the mixture or if there is a deficiency of intermediate [medium] aggregates, mechanical properties of the mix, as well as placing and finishing will result in an inferior product. Eventually, the mechanical and physical properties of the concrete will continue to deteriorate creating additional problems.
The quantity of the fine aggregate and coarse aggregates in a mixture must be in balance with one another so as to create a particle size distribution to produce a specified accumulated density. However, selection of the aggregates is or sometimes not always consistent. Accessibility, environmental mandates and the cost to import supplementary natural or artificial intermediate aggregates are issues that must be addressed so that a maximum optimized concrete can be produced economically for performance, durability, and structural construction methodology.
Light Weight Aggregates
Introduction
Lightweight aggregates are defined as aggregates of low density, such as: (a) expanded or sintered clay, shale slate, diatomaceous shale, perlite, vermiculite or slag; (b) natural pumice, scoria, volcanic cinders, tuff, and diatomite; or (c) sintered fly ash or industrial cinders used in lightweight concrete.
Definition
Lightweight-aggregate concrete has a substantially lower bulk density than that of concrete made with gravel or crushed stone. This lower bulk density results from using lightweight aggregates, either natural or manufactured. Many types of aggregates are classified as lightweight, and are used to produce concretes with a wide range of densities and strengths.
These include low-density concretes, structural lightweight concretes, and moderate-strength lightweight concretes, each of which is discussed in more detail in the following, along with the types of aggregates normally used in its production.
Low-density concretes
Low-density concretes, whose density seldom exceeds 800 kg/m3 (50 lb/ft3), are used chiefly as insulation. While their thermal insulation values are high, their compressive strengths are low, ranging from approximately 0.7 to 7.0 MPa (100 to 1000 psi). Vermiculite and perlite are the most common aggregates used in this type of concrete. Vermiculite is a micaeous mineral. When heated, layers of combined water in the mica’s laminar structure are converted to steam, and the material disintegrates by peeling off in successive layers, each of which swells and opens up. Perlite is a volcanic glass containing enough combined water so that when it is heated quickly, the internally generated steam expands violently and breaks the material into small expanded particles. The bulk density of vermiculite and perlite ranges from 96 to 192 kg/m3 (6 to 12 lb/ft3).
Structural lightweight concrete
Structural lightweight concretes have densities ranging from 1360 to 1920 kg/m3 and minimum compressive strengths of 17.0 MPa. Their insulating efficiency is lower than that of low-density concretes, but substantially higher than that of normal weight concretes. The most common aggregates used in this type of concrete are expanded slags; sintering-grate expanded shale, clay, or fly ash; and rotary-kiln expanded shale, clay, or slate.
Sintering can produce either crushed or pelletized aggregates. Crushed aggregates are produced using raw materials that either contains organic matter that can serve as fuel, or have been mixed with fuel such as finely ground coal or coke. The raw materials are pre moistened and burned so that gases are formed causing expansion. The resulting clinker is then cooled, crushed, and screened to the required gradation. The finished product tends to be generally sharp and angular with a porous surface texture. Pelletized aggregates are produced by mixing clay, pulverized shale, or fly ash with water and fuel; pelletizing or extruding that mixture; and then burning it. The resultant aggregate particles are generally spherical or cylindrical.
In the rotary kiln process, raw material such as shale, clay, or slate is introduced in a continuous stream at the upper end of a rotary kiln. As the material slowly moves toward the burner at the lower end, the heat, slope, and slow rotation of the kiln cause the material to soften and to trap internally forming gases into an internal cellular structure. In one variation of this process, the expanded (bloated) material is discharged, cooled, and then crushed and screened to the required aggregate gradations. The resultant particles tend to be cubical or angular in shape and have a porous surface texture. Alternatively, before being introduced into the kiln, the raw material is pre sized by crushing and screening, or by pelletizing. The individual particles then bloat without sticking together. They tend to have a smooth shell over a cellular interior. These two variants can be combined to produce coarse aggregate consisting mostly of uncrushed particles, obtained by screening, and fine particles obtained by crushing the fired product.
Moderate-strength lightweight concrete
Moderate-strength lightweight concretes have a density and strength approximately midway between those of low-density and structural concretes, and are sometimes designated as fill concrete. They are usually made with pumice or scoria aggregate. Pumice is spongy lava from which steam or gas escaped while it was still hot, and has tube-like, interconnected void pores. Scoria is a volcanic cinder whose pore structure consists mostly of isolated voids.
Properties
Due to their cellular structure, the bulk specific gravity of lightweight aggregates is lower than that of normal weight aggregates. The bulk specific gravity of lightweight aggregates also varies with particle size, being highest for fine particles and lowest for coarse particles. This is because crushing destroys larger voids, producing finer aggregates with lower porosity. With present ASTM methods, it is difficult to accurately determine bulk specific gravity and absorption for lightweight aggregates, due to problems in consistently achieving a saturated surface-dry state. Thus, in designing concretes using lightweight aggregates, a specific gravity factor is used instead of the bulk specific gravity. This factor is found in the same way as the bulk specific gravity SSD previously described except that Mass S is the mass of the aggregate at the stockpile moisture, and the mass of the sample in water is measured at a specified number of minutes after immersion. Additional information of specific gravity factors for lightweight aggregates is given in the Appendix of ACI 211.2.
The bulk density of structural lightweight coarse aggregate is normally from 480 to 1040 kg/m3 (30 to 65 lb/ft3), significantly lower than that of normal weight aggregates. The bulk density of structural lightweight fine aggregate is normally from 720 to 1120 kg/m3 (45 to 70 lb/ft3). For aggregates with the same gradation and particle shape, bulk density is essentially proportional to specific gravity. Although aggregates are usually batched by mass, the volume proportion of the aggregate determines the final yield (volume of the resulting concrete). For this reason, the bulk density of lightweight aggregate is generally checked daily. Variations in bulk density are usually due to changes in grading or particle shape, and can cause variations in concrete yield.
Particle shape and surface texture can vary considerably for lightweight aggregates produced by different methods. Particles are usually roughly spherical, but can be quite angular. Surface texture may range from relatively smooth with small exposed pores, to irregular with small to large exposed pores. These characteristics in both fine and coarse aggregates affect the workability, water requirement, and cement content of lightweight-aggregate concrete, just as they affect concrete made with normal weight aggregates.
In general, grading requirements for lightweight aggregates are similar to those for normal weight aggregates. Lightweight aggregates, however, require a larger percentage by mass of material retained on fine sieve sizes because the specific gravity increases with the decreasing particle size.
Thus, to get an adequate volume of smaller particles, the percent by mass of these particles must be increased. Grading requirements for lightweight aggregates are given in ASTM C 330. Maximum size grading designations generally available are 19, 12.5, and 9.5 mm (3/4, 1/2, and 3/8 in.). Sieve analysis is conducted as for normal aggregates, except that the test sample of fine aggregate has a smaller mass, and the mechanical sieving time is only 5 minutes. These modifications are intended to prevent clogging of smaller sieves and to prevent breakage of the more friable particles during sieving. For coarse aggregate, the test sample must be at least 3 L (0.10 ft3) in volume.
Lightweight aggregates, due to their cellular structure, can absorb more water than normal weight aggregates. In a 24-hour absorption test, they generally absorb from 5 to 20% by mass of dry aggregate, depending on the pore structure of the aggregate. Normally, under conditions of outdoor storage in stockpiles, total moisture content does not exceed two-thirds of that value. This means that lightweight aggregates usually absorb water when placed in a concrete mixture, and the resulting rate of absorption is important in proportioning lightweight concrete. For further information on proportioning lightweight concrete, the reader is referred to ACI 211.2, “Recommended Practice for Selecting Proportions for Structural Lightweight Concrete.”
The maximum compressive strength attainable in concrete made with a given lightweight aggregate may depend on the aggregate itself. The concept of “strength ceiling” may be useful in this regard. A mixture is near its strength ceiling when similar mixtures containing the same aggregates and with higher cement contents have only slightly higher strengths. The strength ceiling represents a point of diminishing returns, beyond which an increase in cement content does not produce a commensurate increase in strength. This ceiling is influenced predominantly by the coarse aggregate. The strength ceiling can be increased appreciably by reducing the maximum size of the coarse aggregate for most lightweight aggregates, especially weaker and more friable ones.
Acknowledgements
This paper being is not based on any original research. The author has compiled information from various source material and industry technical literature besides narration of experiences by experts of the construction industry. The material compiled from various references is duly acknowledged.
Reference
Specified Density Concrete published by Light Concrete LLC