Paints - Types and Application Processes
In the present state of deteriorating environmental conditions, treatment of all those surfaces using Paints and Coatings play a vital role. Time has come now to give this sector its due importance and understand the innovations that are going on in the painting technology arena. All these days, paintings and coatings were primarily looked from the aesthetic point of view but not anymore. Built Expressions bureau brings to its readers a consolidated information docket compiled from several documents available from various sources and acknowledges the sources. It is a well known fact that, treated Building surfaces are prone to wear and tear and fade with time. Periodic maintenance is not only a method to preserve the aesthetic appeal but also to protect and enhance the life of the surfaces.
Types of Paints1
Oil Paint
Contains pigments usually suspended in linseed oil, a drier, and mineral spirits or other type of thinner. The linseed oil serves as the binder for the pigments, the drier controls drying time, the thinner controls the flowing qualities of the paint. As the thinner evaporates, the mixture of pigments and oil gradually dries to an elastic skin as the oil absorbs oxygen from the air or "cures". The curing action bonds a tough paint film to the applied surface. Oil paints are used inside and outside and are regarded as the traditional house paint.
Varnish
Varnish contains little or no pigment. It dries and hardens by evaporation of the volatile solvents, oxidation of the oil, or both. Varnish is recommended for both outdoor and indoor applications where a hard, glossy finish that is impervious to moisture is desired. For a satin finish, the gloss varnish surface can be rubbed down with steel wool, or a "satin" varnish can be used. As a floor finish, varnish provides a hard, durable film that will not greatly alter the tone of the wood.
Enamel
Enamel is a varnish with pigments added. Enamel has the same basic durability and toughness of a good varnish. It produces an easy to clean surface, and in the proper formulation, can be used for interior and exterior applications. For the highest quality interior work, an undercoat is required.
Latex Paint
Latex paints are quick?drying, low in odour and thinned with water. They permit the repainting and decorating of a room within a day. Because latex paints set quickly, tools, equipment and spattered areas should be cleaned promptly with warm, soapy water. No special primer is required for interior applications except over bare metal or wood, or over highly alkaline surfaces. Spot-priming with shellac should be avoided because shiny spots will bleed through the latex film. Exterior latex house paint can be applied directly to old painted surfaces. On new wood, it should be applied over a primer. For other surfaces, follow specific label directions.
Water-Reducible Paints
These products are also called "water?base" or "water?borne" paints. They include the well?known latex products, as well as products based on new synthetic polymers. While both groups employ water as the reducing agent, the chemistry of each is different. For example, most latex coatings dry by solvent evaporation or coalescence. The new synthetic polymeric paints dry by a combination of solvent evaporation and chemical cross?linking. Chemical cross?linking frequently requires the blending of two materials (these products are called "two?component" coatings) and a "digestion" time before the coating can be applied. The blending of specific materials results in chemical cross?linking and outstanding performance features, such as mar resistance, scratch resistance, wash ability and stain resistance.
Alkyds
Alkyd finishes are produced in four sheens: flat, semi?gloss, low?lustre and high?gloss. Flat finishes have a velvety texture and are used to produce a rich, softly reflective surface. Alkyd flats can often be applied to painted walls and ceilings, metal, fully cured plaster, wallboard and woodwork without a priming. When required, the primer should be of a similar material. For high alkaline surfaces, an alkali?resistant primer should be used.
Semi?gloss or low?lustre types add just enough sheen to woodwork and trim for contrast with flat?finished wall surfaces. Each offers great resistance to wear and washing. Low?lustre enamels are preferred in such areas as kitchens, bathrooms, nurseries and schoolrooms. Alkyd high?gloss enamels are often used for even greater serviceability and wash ability.
Polyester-Epoxy
Two?component materials that are usually mixed prior to application- Polyester?epoxy combines the physical toughness, adhesion and chemical resistance of an epoxy with the colour retention and permanent clarity of polyester. The film is stain resistant and moisture resistant. Polyester?epoxy is available in gloss and semi?gloss sheens, and can be applied to any firm interior surface. Pot life is a full working day.
Acrylic-Epoxy
Two?component coatings developed by Pittsburgh Paints include Pitt?Glaze Water Base Coatings. Chemically, acrylic?epoxy coatings provide the resistance to staining, yellowing and scuffing of acrylic resins, combined with the toughness, acid and alkali resistance of epoxies. Their performance characteristics are almost equal to those of polyester?epoxy solvent based products and their stain resistance is superior.
Acrylic?epoxy coatings are available in gloss and semi?gloss finishes ? in both clear and pigmented formulations. Colorant can be added to the pigmented products to achieve hundreds of colours. Though priced higher than conventional enamels, acrylic?epoxy coatings offer superior washability, non?yellowing characteristics, and generally 3?5 times longer life, which makes them an outstanding value for interior walls continuously subjected to hard?use conditions.
Epoxy
Epoxy finishes are extremely hard and durable and excellent for demanding applications. They can be used for protecting materials such as steel, aluminium and fibre glass. The paint film dries to a brilliant gloss. The tile-like finish is smooth, easy to clean and lasts for years under the most severe conditions.
Polyamide-Epoxy
Tough, two?component finish with outstanding hardness, abrasion resistance, alkali and acid resistance, and adhesion when dry. Excellent as a concrete floor finish where heavy traffic wears through an alkyd finish in a short time. For exterior applications, polyamide?epoxy will chalk and lose gloss on prolonged exposure; however, film integrity is not lost.
Urethane-Modified Alkyds
One-component finishing material for outstanding abrasion resistance on wood floors, furniture, panelling, cabinets, etc. Good resistance to normal household materials such as alcohol, water, grease, etc. It may yellow to some degree with age.
Acrylic-Urethane Coatings
Recommended for areas that demand superior chemical and stain resistance, plus colour and gloss retention- They are suitable for both interior and exterior application on properly primed steel, aluminium and masonry which are subjected to high acids and alkalinity. These products are designed to be used in commercial and industrial applications but not in homes.
Acrylic?urethane coatings have high performance properties including excellent resistance to salt, steam, grease, oils, many coolants, solvents and general maintenance type machinery fluids. They also have excellent film properties and resistance to scratching, marring and chipping. The tile?like gloss and semi?gloss finishes provide superior corrosion and abrasion resistance, while maintaining excellent gloss and colour retention on exterior exposures for long periods of time. The colour and gloss retention, and chemical resistance of acrylic?urethane coatings will exceed those of conventional high performance coatings. They also dry to the touch faster than any other heavy duty topcoat in the trade sales line.
Aluminium Paint
An all purpose aluminium paint formulated with varnish as the vehicle for aluminium flake pigment- As the paint dries, the aluminium flakes float to the surface, providing a reflective coating. These are generally highly resistant to weathering and also suitable for interior use on wood, metal or masonry surfaces. When formulated with an asphalt base, aluminium paint offers maximum adhesion and water resistance at low cost when applied to asphalt composition.
Shellac
A long standing favorite for finishing wood floors, trim and furniture- Shellac is thinned with alcohol and should be applied in dry, warm air to avoid clouding. It dries dust?free in 15?20 minutes. Shellac can be used as a pre?staining wash coat to obtain an even stain tone on porous or soft wood such as pine. It can also be used to change the tone of an already shellacked surface by tinting it with alcohol?soluble aniline dye. Instead of re?staining, pigmented shellac, also called shellac enamel, is often used as a sealant over stained finishes for a uniform, freshly painted surface.
Paints in the Market5
Emulsion Paints
These are the superior quality of paint formed by mixing oil/water and an emulsifying agent to prevent the combination separating. They have much better ease of application, are washable and have a greater overall decorative appeal. Not only do they have higher coverage than enamels and distempers, they are mostly washable and can be easily applied on concrete and stucco surfaces. As per the interior and exterior painting requirements both interior and exterior emulsion paints exist.
Enamel Paints
Enamels are hard, washable and usually glossy paints. They can be oil based or alkyd based and come in several sheens, from eggshell or low-luster to satin, semi-gloss and high-gloss. They find application not only on metal surfaces but also on interior walls and wooden surfaces.
Distemper Paints
Distempers are durable and economical water based paints The major constituents of distemper include colouring agents, as well as chalk and lime. They have been the main painting substance for decades and still are excellent budget painting solutions. Even the distempers now used are more varied and have special properties.
Primer
A primer is a preparatory coating put on materials before painting. Priming ensures better adhesion of paint to the surface, increases paint durability, and provides additional protection for the material being painted. Different types of surfaces and different types of paints required different types of primers.
Putty
Putties are base coats applied to walls before painting; they provide a protective layer for the expensive paint. Putties are generally non-hygroscopic and resist moisture giving more life to the painting surfaces. Not only do they provide smooth surfaces by levelling undulations, cracks etc but also are helpful in increasing the coverage of the paints applied.
Aluminium Paint
These are paints containing Aluminium blended in a resin base. Despite its name, aluminium paint is actually used to paint a variety of materials, including metals, wood, and masonry. It is long-lasting and durable, and is one of the best types of paint to use around oil, grease, and chemicals. The painted surface offers realistic aluminium finishes, and is highly resistant to rust and corrosion.
Texture Paints
Texture paints are used to create to desired visual effects on the walls. By the use of brushes, rollers, putty knives, trowels and other applications a variety of patterns can be created. Other paints can be applied on the textures to create desired effects. Sometimes, texture paints are tinted prior to application, giving the desired colour. Texture paints also help in covering undulations and levelling surfaces.
Cement Paint
To give a new look for concrete and other cement-based materials, cement paint is the perfect answer. It is a special paint coatings made for masonry and cement-based materials, including concrete, mortar (and brick), concrete block and stucco. Not only it adds to the aesthetics of the wall but also provides a waterproofing coating and can supplement the role of putty.
Methods of Application
Introduction
There are about a dozen different ways to apply paint. Each one is uniquely suited to a particular job. The method of application is largely dependent on the type of coating selected. The most widely used methods of applying protective coatings are brush, roller, conventional (air) spray, conventional (pressure pot) spray and airless spray. The advantages and disadvantages of these methods are briefly discussed below. Other, less widely used methods include trowel, putty knife.
The object in applying a coating is to provide a film which will give protection and/or decoration to the surface being painted. The success of any paint application will be governed by a number of parameters, including: Surface preparation, Film thickness, Methods of application and Conditions during application.
Film Thickness-
An adequate film thickness is essential for the success of any coating system. Under-application will generally result in premature failure. However, the old adage of “the more paint, the better” can be equally dangerous. The gross over-application of modern high technology coatings can lead either to solvent entrapment and subsequent loss of adhesion, or to splitting of primer coats. With the majority of coatings, the limits of acceptable dry film thickness allow for reasonable practical variation, but the specified film thickness should always be the target during application.
The actual dry film thickness recommended for a particular surface will depend on the type of coating system being used and the nature of the surface. Recommended dry film thicknesses for individual products are given on the product data sheets.
Dry Film Thickness Measurement-
If a coating is applied to a steel substrate, previously blast cleaned with abrasive grit or shot, the measurement of its dry film thickness is more complicated than that of a coating applied to a smooth steel substrate. The measurement results are influenced by the profile of the abrasive blasted surfaces which changes from point to point, the construction of the measuring equipment, (e.g. size of the probe) and dry film thicknesses to be measured. Some variations exist in methods of DFT measurement; DFT gauges can be calibrated on smooth or blasted steel panels and a correction factor for surface profile may or may not be considered. ISO 2808:2007, ISO 19840:2004 and SSPC-PA2 are accepted standards for measuring DFT.
The DFT is typically measured using a non-destructive magnetic gauge, which will give a value measured from the surface of the coating to the magnetic plane within the surface profile. The magnetic plane is the theoretical point within the surface profile that the DFT gauge sees as being the average position of the substrate. When thin films are being applied care should be taken to consider the surface profile whereby some of the coating is being used to fill in the profile. For blast primers and coatings of less than 25 microns, measurement over the blasted surfaces is not meaningful.
Methods
1. Brush Application
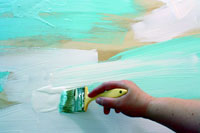 |
Brush application should always be undertaken using an appropriately sized, good quality synthetic or natural fibre brush compatible with the product being applied. This application technique is relatively slow and is generally used for coating small areas with decorative paints and for surface tolerant primers, where good penetration of rusty steel substrates is required. |
It is particularly suitable for the application of stripe coats and for coating complex areas where the use of spray methods would lead to considerable losses due to overspray and associated dry spray problems.
Note that most high build coatings are designed for application by airless spray; high film build will generally not be achieved by brush application. In general, twice as many coats will have to be applied by brush to achieve a similar build when compared to airless spray.
Brush application requires considerable care when applying non-convertible coatings over one another, e.g. chlorinated rubber over chlorinated rubber, or vinyl on top of vinyl. In these cases, the solvents in the wet coat readily re-dissolve the previously dry bottom coat. Even a mild degree of the brushing out normally given to topcoats will cause pick-up of the previous coat and result in a very poor finish. Even, light strokes should be used in these circumstances, covering a particular area with one or two brush strokes, and on no account working the bristles into the previous coat.
2. Roller Application
Roller application is faster than brush on large, even surfaces and can be used for the application of most decorative paints. However, control of film thickness is not easily achieved. As with brush, high film-build will generally not be attained. Care must be taken to choose the correct roller pile length, depending on the type of paint and degree of roughness of the surface. Typically, phenolic core rollers should be used fitted with a smooth to medium pile roller cover and the roller cover should be pre-washed to remove any loose fibres prior to use.
3. Air Spray
Conventional-This is a widely accepted, rapid method of coating application in which paint is atomised by a low pressure air stream. Conventional air spray equipment is relatively simple and inexpensive, but it is essential to use the correct combination of air volume, air pressure and fluid flow to give good atomization and a paint film free from defects. If conventional spray application is not controlled correctly, large losses of paint can result from overspray and rebound from the surface, in addition to problems such as poor flow, sagging and pin holing. The major disadvantage of conventional air spray is that high build coatings can generally not be applied by this method, as most paints have to be thinned to a suitable viscosity for satisfactory atomisation, and so lose their high build properties.
Pressurized- The airspray gun uses air at 30 to 85 pounds per square inch (psi) to atomize the paint into a fine spray. This produces a smoother finish, and can be used on many surfaces. Air spraying is versatile; the operator can vary the air pressure, air volume, paint pressure, and spray pattern. It is much faster than painting by hand unless a lot of masking is required for the job. But air spraying does produce a lot of overspray (the paint that misses the intended target), and preparation and clean-up take more time.
A High Volume Low Pressure (HVLP) spray gun uses a higher volume of air at only 10 psi. This reduces the overspray and increases the transfer efficiency. It is portable and easy to clean, and has a lower risk of blowback to the worker. However, the atomization may not be good enough for fine finishes and production rates when using HVLP may not be as high as with conventional spraying.
4. Airless Spray
This method uses paint under high pressure, 500 to 6,500 psi. Airless spraying has several distinct advantages over air spray–it is twice as fast, produces a higher film build, is more portable, cuts overspray by more than half, and is thus cleaner and more economical. But airless spray is limited to painting large areas, requires a different nozzle to change spray patterns, the nozzle tends to clog, and the nozzle can be dangerous to use or to clean because of the high pressures involved.
5. Electrostatic Spraying
The differences between this and air spraying are that the electrostatic gun has an electrode at the nozzle and the object to be painted is grounded. The electrode runs 60,000 volts through the paint at 225 microamperes. The charged paint is attracted to the grounded object. This requires less pressure, produces little overspray, and uses relatively little paint. Electrostatic guns are good for painting oddly shaped objects. They also produce a uniform coat because the paint itself acts as an insulator; once the object is covered, it can take no more paint. The disadvantages are: only one coat is possible, only conductive materials can be painted; it’s more expensive, slower, has higher maintenance costs, is limited to chargeable paints, and the surface of the object must be extremely clean. Because the gun uses electricity, this method presents a possible shock hazard.
6. Powder Coating
This is a variation of electrostatic spraying. The difference is that what is sprayed is a paint powder. The object is then baking, and the powder melts into a smooth, durable coat. Overspray can be reused, and no other pollutants are created or released because the powder has no solvents in it. The equipment for powder coating is expensive, so it may be economical for only larger businesses. A variation of this is plasma powder coating. The powder is fed into an extremely hot gas stream and is then sprayed at the object. Plasma powder coating is for large objects that can’t fit into a conventional curing oven. Overspray cannot be reused because it hardens. Another variation is flame sprayed powder coating, where the powder is melted with a high temperature flame. Again, it is for large objects and overspray cannot be reused.
7. Rotary Atomizing
Another variation of electrostatic painting, rotary atomizers use centrifugal force, not air or hydraulic pressure, to drive the paint out of the nozzle. The atomization of this method is excellent, as is the transfer efficiency. This method can also be used with paints of different viscosity. Cleanliness is especially important to this method. Rotary atomizers can present a fire and safety hazard.
8. Dip Coating
With this process, parts are dipped into a vat of paint. This allows for high production rate and transfer efficiency, and it requires relatively little labour. The effectiveness of dip coating depends greatly on the viscosity of the paint, which thickens with exposure to air unless carefully managed. Dip coating is not suitable for objects with hollows or cavities, and generally the finish is of lower quality.
9. Flow Coating
With this method, parts are carried on a conveyor. Anywhere from 10 to 80 streams of paint coat the parts. This system has the advantages of dip coating, along with low installation costs and low maintenance requirements. The quality of the finish is also about as good as with dip coatings.
10. Curtain Coating
Instead of many streams of paint, curtain coating uses a waterfall flow of paint to coat parts on a conveyor belt. Curtain coating has high transfer efficiency and covers parts uniformly, but is suitable only for flat work. The quality of the finish is highly dependent on the viscosity of the paint.
11. Roll Coating
Paint is applied to auxiliary rollers, which then transfer the paint to the application rollers, which run across the part. This method has high transfer efficiency and high production rates, but is limited to flat work.
12. Electro coating (or Electro deposition)
Parts to be painted are dipped into the paint. Then a current is applied, which electrically deposits the paint on the object. Parts are made primarily of steel. The transfer efficiency of electro coating is over 90%. High production rates are possible, and production can be automated. However, this method is costly and requires a lot of energy. Also, employees need high level training to use this system.
13. Auto deposition
This is a dip process where organic paints are precipitated onto iron, steel, zinc and zinc-alloy plated objects. It is effective for its anti-corrosion properties and coverage of objects. Auto deposition also uses water-borne paints and uses no electricity. But auto deposition produces a dull or low gloss finish and has few available colours.
References:
- Glossary of Industrial terminologies
- Perfection in Protection-Guidelines
- WMRC Fact Sheets
- International Paint Limited-Akzonobel Document.
- JNPaints.com