Rapid Affordable Mass Housing using Glass Fibre Reinforced Gypsum (GFRG) Panels
by- Prof. Devdas Menon & Prof. A Meher Prasad, Department of Civil Engineering IIT Madras
GFRG is the abbreviation for Glass Fibre Reinforced Gypsum. It is a new building panel product, known as Rapidwall®, introduced recently in India, and manufactured by Rashtriya Chemicals & Fertilizers (RCF), Mumbai and FACT Ltd, Kochi. It is made essentially of gypsum plaster, reinforced with glass fibreovings. This product, suitable for rapid mass-scale building construction, was originally developed and used since 1990 in |
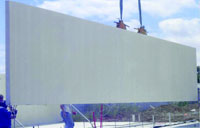
|
Australia by Rapidwall Building Systems. GFRG is of particular relevance to India, where there is a tremendous need for cost-effective mass-scale and rapid housing, and where gypsum is abundantly available as an industrial by-product waste. In India, the panels are made from processed phospho-gypsum (recycled industrial waste from the fertilizer industry.
Gypsum plaster has been used extensively in the building industry worldwide to provide high quality architectural and decorative finishes, and also in the production of plasterboard (12 mm thick) for interior partition walls. Until recently, gypsum plaster was considered to be too weak to be used for load bearing walls. The Australian technological breakthrough of combining glass fibre strands with gypsum plaster, produced in an energy-efficient fluidized bed calcining process, resulted in GFRG wall panels, which had the desired properties of strength and water resistance. The ‘Rapidwall’ panel is the world’s largest load bearing, light-weight, pre-fabricated building panel – 12m long, 3m high and 124 mm thick with modular cavities, as shown in Figure 1. The cellular cavities are formed between the two outer skins (15 mm thick), which are inter-connected by solid ‘ribs’ (20 mm thick), spaced at 250mm intervals. These cavities can be conveniently filled with concrete and reinforced with steel, if required, to provide for additional strength and to |
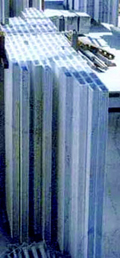
|
improve ductility. They can also be used to conceal wiring, piping, insulation, etc. The panels can be factory-cut to required room sizes and with openings for doors and windows.
In Australia, several buildings have been built using the Rapidwall technology, where the panels were used only as walls, resisting gravity loads. The floors were made of conventional reinforced concrete slabs.
Since 2003, our research group at IIT Madras were involved in exploring the use of these GFRG panels to address the needs for rapid and affordable mass housing in India. We extended the use of the GFRG panels as floor (and roof) slabs and staircases, with reinforced concrete embedded in some of the cavities, along with a layer of 50mm thick screed concrete on top. The unfilled cavities in the GFRG floor panels can be effectively used to house various building services such as electrical conduits and piping. The use of GFRG panels for walls, floors and staircases, appropriately designed for composite action with reinforced concrete, with tie beams at all the wall-floor junctions, provides for a complete GFRG building system. This has the advantages of not only rapid construction, but also cost effectiveness and energy efficiency, in terms of using less cement, sand, steel and water, and recycled use of industrial waste. Tests have established that the panels have the required resistance to water and fire.
In India, unlike Australia, we also have to deal with earthquake resistant design, as more than fifty percent of our population lives in seismically prone areas of moderate to severe earthquakes. Hence, the GFRG building system has to be designed to meet the requirements of the prevailing standards of seismic resistance. Our group had conducted extensive studies on the use these panels as structural members for earthquake resistant design, and a detailed design methodology has been developed. The research work has resulted in two PhD theses, and two PhD scholars are currently continuing the R&D efforts. The Department of Science and Technology, Government of India, had recently awarded a research grant of Rs 1.32 crores to complete the research work and bring it to a stage of technology transfer.
The panels may be unfilled, partially filled or fully filled with reinforced concrete, as per the structural requirement. Experimental studies and research have shown that GFRG panels, suitably filled with reinforced concrete, possess substantial strength to act not only as load-bearing elements, but also as shear walls, capable of resisting lateral loads due to |
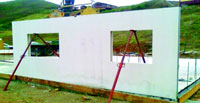
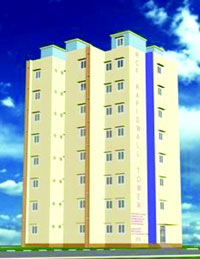
|
earthquake and wind. It is possible to design such buildings up to ten storeys in low seismic zones (and to lesser height in high seismic zones). However, such construction needs to be properly designed by a qualified structural engineer. Manufacture of GFRG panels with increased thickness of wall (150 mm) and skins (20 mm) can facilitate construction of taller buildings.
Based on the research work carried out at IIT Madras, and the research reported elsewhere (Australia and China), Building Materials & Technology Promotion Council (BMTPC), Government of India, has accorded approval of GFRG panels for construction in India. However, to facilitate such construction, it was felt necessary to bring out appropriate design and construction manuals that meet the statutory requirements of relevant Indian Standards, and this work has been entrusted to IIT Madras. Recently, BMTPC published a GFRG / Rapidwall Structural Design Manual prepared by IIT Madras. A Manual of Waterproofing of GFRG / Rapidwall Structures is currently under publication by BMTPC. The proposed waterproofing method envisages complete protection of the building envelope, and needs to be applied carefully using trained workers.
The GFRG building system can be designed to provide affordable mass housing for a wide variety of applications – from single storey to medium rise (multi-storey) structures (Figure 3) – in rural, suburban and urban settings. It is necessary to plan meticulously all the details related to the design and construction, especially issues related to optimal use of the GFRG panels, concrete and reinforcement, as well as issues related to transportation, erection, provision of services and deployment of manpower and equipment. Ideally, plants manufacturing GFRG panels need to be set up in many regions, to minimize transportation costs, and to cater to the immense and urgent need for mass housing in India – for which the GFRG building system holds promise as providing an effective solution, when scaled up in its application.
|
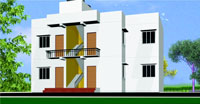
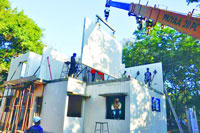
|
We had designed an 8-storeyed GFRG building for 32 flats (carpet area 32.7 sq.m. per flat) for construction at the RCF campus at Mumbai. Comparison of this building with a conventional RC framed building revealed significant savings in cost, manpower and material. For the same carpet area, the GFRG building needs 12% less built-up area and 75% less time for construction. The weight of the structure reduces by close to 60%, also reducing the foundation costs and design earthquake forces. The savings in terms of steel and concrete consumption are 24% and 63% respectively in the superstructure. Additionally, there is a tremendous saving in plastering.
With the idea of demonstrating this building system using the technology developed, a two-storey GFRG demonstration building is currently being constructed at the IIT Madras campus, on a built-up area of 1981 sq.ft. It is a model housing apartment, combining four flats (two for the Economically Weaker Section and two for the Lower Income Group), which can be replicated for mass housing, vertically and horizontally. It is also planned to demonstrate the completion of the entire superstructure and render it fit for occupation, within 30 days after the laying of the foundation. The use of prefabricated light weight (43 kg/m2) GFRG panels for the entire building system implies not only faster construction time, but also reduced labour and safer working environment. Also, the cost of completed construction with all amenities is reduced to around Rs. 1250 per sq. foot. In an effort to test this technology and its durability, the team at IITM will conduct a series of experiments, including filling the roof with water.
During the construction of the demonstration building, we also conducted a short-term course to train 35 engineers on the design and construction aspects of GFRG building systems.