Riverside Museum of Glasgow
The Creative Apotheosis
Zaha Hadid, founder of Zaha Hadid Architects and the winner of the Pritzker Architecture Prize (considered to be the Nobel Prize of architecture) is internationally known for both her theoretical and academic work. Each of her dynamic and innovative projects builds on over thirty years of revolutionary exploration and research in the interrelated fields of urbanism, architecture and design. Hadid’s interest lies in the rigorous interface between architecture, landscape and geology as her practice integrates natural topography and human-made systems, leading to experimentation with cutting-edge technologies. Such a process often results in unexpected and dynamic architectural forms.
Zaha Hadid shares with Built Expressions about her work on the fascinating Riverside Museum project.
Introduction
Glasgow's Riverside Museum is the UK's newest and most exciting visitor attraction. Located on the banks of the River Clyde, the world-class Riverside Museum is a marvel of design and engineering. Moored outside is the 19th-century sailing ship Glenlee, creating an iconic destination that explores our histories and embraces our future. The £74 million museum is Hadid’s first major public commission to open in the UK. Inside the Zaha Hadid-designed museum, visitors are awed by the stunning displays, packed with fascinating exhibits, high-tech and hands-on interactive, and inspiring and moving stories. The main contractors for the project were BAM Construct UK Ltd with a range of trade subcontractors including the services installations being delivered by BBESL's team of Jordan Kerr, Gordon Ferguson & Jamie Will and FES, project management being the responsibility of Capita Symonds and Buro Happold providing Resident Engineering Services.
Although containing approximately the same floor space as the previous museum facility at 7,500 sq m, it creates a more environmentally stable home for Glasgow's significant Transport Technology collections. The building also houses a workshop and office space for the Clyde Maritime Trust. The location of the museum is on the site of the former A. & J. Inglis Shipyard within Glasgow Harbour, on the north bank of the River Clyde and adjacent to its confluence point with the River Kelvin. This site enables the Clyde Maritime Trust's SV Glenlee and other visiting craft to berth alongside the museum. With more than 3,000 objects on display, from skateboards to locomotives, paintings to prams, velocipedes to voiturettes, there is something for visitors of all ages.
Design Principle
"The design is a sectional extrusion, open at opposing ends along a diverted linear path. This cross-sectional outline is a responsive gesture to encapsulate a wave or 'pleats'. The outer 'pleats' are enclosed to accommodate support services and the 'black box' exhibits. This leaves the main central space column-free and opens, offering greatest flexibility to exhibit the museum's world-class collection," states Ar. Zaha Hadid, founder, Zaha Hadid Architects.
The Riverside Museum is a fantastic and truly unique project where the exhibits and building come together at this prominent and historic location on the Clyde to enthuse and inspire all visitors. The design, combining geometric complexity with structural ingenuity and material authenticity, continues Glasgow's rich engineering traditions and will be part of the city's future as a centre of innovation.
Structural System
The structure's appearance is very elegant through its structural design, when asked about the measures taken on steelworks Ar. Zaha Hadid explains "The technical challenges overcome by the steelwork designers and steelwork contractors were formidable, and it is a pity that the large structure will be mainly concealed. Nevertheless the contribution to the building is both crucial and praiseworthy.
The form of the roof structure is roughly z-shaped in plan with structural mullions at each end that not only support the roof, but also allow the glazed end façades to be supported without the need for any secondary members. In section the roof is a series of continuous ridges and valleys that constantly vary in height and width from one gable to the other with no two lines of rafters being geometrically the same. Generally the cross section is a pitched portal frame with a multi pitched rafter spanning between the portal and a perimeter column. There are also curved transition areas where the roof changes direction in plan".
The rafters themselves are not straight in plan but a series of facets that change direction in each valley. To accommodate these changes in line and to facilitate the connection of any incoming bracing and other members, the rafters at the ridges and valleys are joined at the surface of a cylindrical 'can'. The majority of these 'cans' were truly vertical in the preset geometry of the roof, however where the relative slopes either side of the ridge or valley would have generated inordinately long oblique cuts the 'cans' were inclined to bisect the angle between adjacent rafters. The diameter of most of the 'cans' was able to be standardized but, in cases of extreme geometry or where the sheer number of incoming members dictated, a larger diameter had to be used to allow all the incoming members to be welded directly to the 'can' wall. The most complicated valley connection had 10 incoming members that necessitated the use of a 1.0m diameter 'can' over 1.5m tall. By using vertical 'cans' in the valley positions a standard connection between the tops of the tubular support props and the roof structure was designed. This consisted of a thick circular base plate to the 'can' with a blind M24 tapped hole in its centre, thus allowing an 80mm diameter tapered shear pin to be bolted directly to the base of the 'can'.
Adding to that she also shares, "The accuracy of fabrication was achieved by using a combination of shop jigs and EDM setting out techniques. All the complex rafter members were assembled in shop jigs whilst the geometry of the more simple members was set using EDM’s that were able to set the positions of certain critical splice connection holes. This was made possible by adding virtual "wires" through the centres of some of the holes during the X-Steel modeling. These wires allowed the EDM operator to check its end position in space when a circular prism was placed in the hole. Using this technology it was possible to accurately position the remote end of a steel member to ± 2mm in any direction".
The more complex members were assembled using shop jigs. These jigs were created by extracting a single member (assembly) from the X-Steel model, rotating it in space to create a single reference plane and then modeling in a secondary steelwork “frame” that the individual pieces (fittings) of the assembly could either be supported on or bolted to. The whole of the building structure is supported on piles with none of the slabs having been designed as ground bearing. The columns are generally founded on individual pile caps with the slab spanning between individual piles so to allow the erection of the roof to be carried out from within the footprint of the building. The ground floor slab was designed to accommodate multiple 10.0 tone loads at a minimum of 1.8m centers.
Facade
The facade is the most vital attraction of every unique structure; it is the effort of the engineer who designs the façade very evidently to add more beauty to the whole structure. "Buro Happold has used a rigorous methodology to resolve the inter-connected issues involved to design and efficient facade for the Riverside Museum. The facade engineers have worked with enormous effort to bring the benefits of high-level technical knowledge to the design of the envelope. With sustainability playing a crucial role in the performance of the structure, the engineers have drafted a design according to the environmental behavior of different facade designs using advanced techniques such as thermal modeling, wind analysis, acoustic design, solar and glare studies," she adds.
After an in depth analysis on the facade design on the various aspects of its requirements, the engineers were able to deliver a façade with natural lighting, shading, ventilation, solar gain, wind flow and weather proofing, high performance facade to the structure.
Roof Design
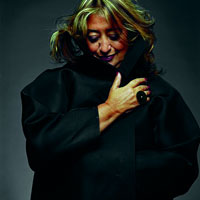 |
The zigzag roof, comprising pleated steel peaks and troughs, is clad with 15,000 sq m of zinc panels and is braced by a series of inclined steel trusses. The 2,500-metric-ton roof spans 80 m without columns, follows the S shape of the structure, and is supported by mullions at the facades. Buro Happold designed the roof cladding to withstand wind and snow loads. Steel trusses create column-free spaces for uninterrupted exhibit areas and circulation paths. The roof is a guide for people to locate internally within the exhibition space. Visitors can be led intuitively by the flow of the roof. Pleated folds hanging from the steel trusses form the majority of the ceiling, and these presented a significant engineering challenge.
|
Interiors
The museum reveals the rich and varied stories of Glasgow's great achievements and vibrant spirit; of technological breakthroughs and heartbreaking tragedies; of local heroes and global giants. Many of these tales are told through audiovisual displays, hands-on interactive and digital touch screens. The displays will be accessible and many are designed to engage children and young people and to give a better experience for disabled visitors.
"The museum's major attractions have been designed and built into the structure of the building – with some arriving before the completion of the structure, such is their size. Highlights include, the Wall of Cars, the hanging Bicycle Velodrome, South African Locomotive, No9 Tank Engine, Motorbike Deck, Ship Launch Show, the Rest and Be Thankful, and three re-created period streets. As well as the old, there are more recent star attractions, including Graeme Obree’s hand-made bikes which made him a world-champion and the late Colin McRae’s Subaru Impreza that he drove to win the World Rally Car Championship. Danny MacAskill became a YouTube sensation after the release of his terrifying video Way Back Home. At the museum, visitors can see the bike made famous through gravity defying stunts and social media," shares Ar. Zaha Hadid.
Lighting System
The award-winning Concord Beacon Muse from Havells-Sylvania has helped to create an energy-saving, high performance lighting display at the Riverside Transport Museum in Glasgow. Used to showcase the various displays in the Modern Street area, eighty two Beacon Muse fittings were chosen for their long life, low energy and optical flexibility. The new scheme provides dynamic accent lighting and helps transport visitors back in time.
The lighting engineers used the versatile spotlight to selectively highlight the displays illuminating cars, bicycles, miniature models, car parts and artworks. Conservation levels applied to all the exhibits so protecting the artwork from light exposure damage was essential. The low UV from the LED source and an on-board dimmer potentiometer from the Beacon Muse meant to comfortably handle all situations.
Fire Safety
Smoke vent and access solution provider Bilco UK has equipped the Riverside Museum with fire safety products. Bilco supplied smoke vents, an access hatch and related equipment for the roofing areas of the wave-shaped transport and travel museum in Glasgow, which is part of a £74million development on the city's waterfront. An aluminum single-leaf thermally-enhanced roof access hatch (ME-50T) was modified by Bilco to fit the 46 degree sloping roof. The hatch allows access to the roof for cleaning and maintenance activities. Smoke vents were supplied with equipment including control panels and smoke detectors.
In terms of design Ar. Zaha Hadid has specified her signature touch to the complete structure of the museum. The presence of the ship beside the museum is a dominant sign of attraction to the visitors. Moreover the artifacts present in the museum have created a path of learning to the public. Thus, the Riverside Museum of Glasgow is a remarkable place of historical knowledge to its visitors.
EOM
Box Item
Size : 11,300m²
Built up area : 11,000 SqM
Exhibition Area: 7,000 SqM
Site Area: 22,400 SqM
Footprint Area: 7,800 SqM
Client: Glasgow City Council
Design: Zaha Hadid Architects
Project director: Jim Heverin
Project architect: Johannes Hoffmann
Structural engineer: Buro Happold, London - Wolf Mangelsdorf, Andrew Chan, Franck Robert, Tim Kelly
Services: Buro Happold, Glasgow - Scott Baird, George Reilly
Acoustics: Buro Happold, Bath - Lawrence Hughes
Fire safety: FEDRA, Glasgow - Brian Morrell
Cost consultant: Capita Symonds - Eric Gordon
Project management: Capita Symonds - George Webb, John Jackson