Self Curing Concrete - A Futuristic Technology
Bharathi Ganesh, Dr. H. Sharada Bai
Curing of concrete is one major area that lacks due attention and due importance
in the construction field, especially in India. Durability, quality, performance
of concrete structures and its longevity is at stake due to lack of awareness of
the importance of curing of concrete. New developments in curing of concrete are
on the horizon throughout the world. In the next century, mechanization of the placement,
maintenance and removal of curing mats and covers will advance as performance-based
specifications quantify curing for acceptance and payment. In addition, effective
sealants and compounds that prevent the loss of water and promote moist curing conditions
of concrete will be in high demand. Self-curing technology should become available
commonly in the not-too-distant future.
Consumption of Water for construction
With the current debate about global warming in the world, the interest to save
water and reduce water footprint for goods and services is a critical issue that
requires more attention and investigation. Freshwater shortage is becoming more
and more a serious problem for the world. Construction Industry is one of the major
consumers of world's water resources. Can the construction industry look at
using the available water more judiciously? Or from another angle, can lesser water
be used for construction work, without sacrificing design specifications and quality?
The construction sector is very demanding in terms of water use,
it was noted that the construction of a 100,000 sq. ft. multi-storey structure can
require about 10 million litres of water for production, curing and site development
activity. A double lane flyover can consume 70 million litres of water on the same
scale. (Ref:
How much water should buildings consume- Online edition of
India's National Newspaper 'The Hindu' Saturday, Feb 07, 2004). So it is the time
now, we need to adapt and adopt newer and newer technologies, that contribute to
the sustainability in construction. Internal/self curing of concrete is one such
technology.
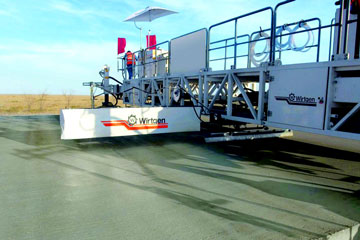 |
Curing is the process of controlling the rate and extent of moisture loss from concrete
during cement hydration. It may be either after concrete has been placed in position
(or during the manufacture of concrete products), thereby providing time for the
hydration of cement to occur. Since the hydration of cement does take time
days and even weeks rather than hours, curing must be under taken for a reasonable
period of time if the concrete is to achieve its potential strength and durability.
Curing may also encompass the control of temperature since this affects the rate
at which cement hydrates. The curing period may depend on the properties required
of the concrete, the purpose for which concrete is to be used and the ambient conditions,
ie the temperature and relative humidity of the surrounding atmosphere.
As may be seen that concrete allowed to dry out without curing achieves only 40%
of the strength of the same concrete water cured for the full period of 180 days.
Even three days water curing increases this figure to 60%, whilst 28 days water
curing increases it to 95%. Keeping concrete moist is therefore, a most effective
way of increasing its ultimate strength.
Concrete that is allowed to dry out quickly also undergoes considerable early age
drying shrinkage. Inadequate or insufficient curing is one of main factors contributing
to weak, powdery surfaces with low abrasion resistance. The durability of concrete
is affected by a number of factors including its permeability and absorptivity,
result of lack of curing. These are related to the porosity of the concrete and
whether the pores and capillaries are discrete or interconnected. Whilst the number
and size of the pores and capillaries in cement paste are related directly to its
water- cement ratio, they are also related indirectly to the extent of water curing.
Long time water curing cause hydration products to fill the pores and capillaries
present either partially or completely in turn to reduce the porosity of the paste.
Curing is designed primarily to keep the concrete moist by preventing the loss of
moisture from the concrete during the period in which it is gaining strength. Curing
may be applied in a number of ways using traditional methods or unconventional methods.
Conventional Curing Methods
The traditional methods of curing generally adopted in the field are:
- Ponding
method
- Ponding is a quick, inexpensive and effective form of curing
when there is a ready supply of good ‘dam’ material (eg. clay soil),
a supply of water. Ponding does not interfere with subsequent building operations.
- Formwork
- Leaving formwork in place is often an efficient and effective method
of curing concrete.
- Plastic
sheeting
- Plastic sheets or other similar materials form an effective barrier against
water loss provided they are kept securely in place and are protected from damage.
Their effectiveness is very much reduced if they are not kept securely in place.
The movement of forced draughts under the sheeting must be prevented when plastic
sheets are used.
- Water
Curing - General
Water curing is carried out by supplying water to the surface of concrete in a way
that ensures that it is kept continuously moist. (Spraying or sprinkling water).
- Fog curing
- Fine spray or fog of water can be used an efficient method of supplying
additional moisture for curing during hot weather, helps to reduce the temperature
of the concrete.
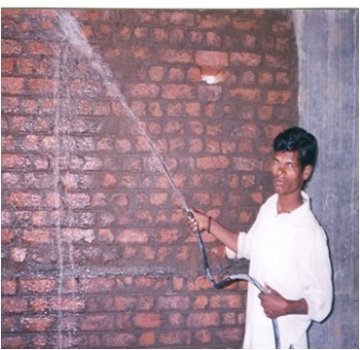 |
Sprinkling of water at regular intervals
for vertical Surfaces
Curing by Ponding
Ponding method of water curing
Wet coverings - Fabrics such as hessian
or materials such as sand can be used like a 'mulch' to maintain water on the surface
of the concrete. On flat areas, fabrics may need to be weighed down. Also, it is
important to see that the whole area is covered. Wet coverings should be placed
as soon as the concrete has hardened sufficiently to prevent surface damage.
Wet coverings & Formwork
The most appropriate means of curing may be dictated by the site conditions or the
construction method. The choice of method depends on the structural member being
cured, as each method offers its own advantages. However, Curing is one major area
that lacks due attention and due importance in the field, especially in India!
An alternative solution to overcome this is to adopt of unconventional
methods for curing of concrete.
Plastic sheeting
Membrane Forming Curing Compounds
Unconventional Curing Methods
These are long awaited engineering techniques that make the post construction processes
and maintenance much simpler and easier. They are much needed techniques and to
be adopted in field, when,
- The quality water resource available for construction is less
- Cost of obtaining water with desired quality is expensive
- Hot weather regions where large quantity of water is needed for
curing
- At all the sites where curing is given least importance
and curing is ignored which make the structure suffer in its quality and strength
parameters.
- Membrane Forming Curing
Compounds - Curing membrane is an isolating barrier for reducing
the water evaporation from the exposed surface of concrete, which inhibits and delays
water evaporation from the surface. Curing compounds are liquids
which are usually sprayed directly onto concrete surfaces and which then dry to
form a relatively impermeable membrane that retards the loss of moisture from the
concrete. Their properties and use are described in AS 3799 Liquid Membrane forming
curing compounds for concrete.
- Self Curing of Concrete -
Self curing is a curing system, introduced during 1990’s with the introduction
of chemical admixture which can reduce water evaporation in the set concrete, providing
water internally resulting in 'self curing'. Hence
the name Self Curing Concrete'. In essence, the existing curing techniques require
'external actions' involving curing concrete from 'outside in'. On the other hand
'internal curing' is the one where curing
is from 'inside out' (C. S. Viswanatha 2008).
Of the two methods, the former has been in practice for over a decade because of
its simplicity of implementation. However Self Curing Concrete is an interesting
concept and is yet to be successfully adopted in the field. Here it is intended
to present few aspects of Self curing concrete.
Self Curing or Internal Curing
Self curing of concrete takes place by means of internal curing where "Internal
Curing refers to the process by which the hydration of cement occurs because of
the availability of additional internal water that is not part of the mixing Water."
- Definition as per ACI-308 Code.
Hydration of cement is aided by additional internal water that is not part of the
mixing water, supplied within the concrete matrix through Super Absorbent Polymers
(SAP) or Partial replacement of fine aggregate with structural lightweight aggregate
(fine and coarse) of high absorption capacity that are incorporated into the concrete
while mixing as an admixture. They inhibit moisture loss and thereby improve long
term strength and reduce drying shrinkage. They have been used in tunnel linings
and underground mines to provide at least partial curing when traditional methods
are difficult or even impossible to employ. Internal curing compounds are technology
yet to get popularized and care should be taken when utilized.
Materials used for self curing effect
Internal water curing or self curing could be achieved using one of the following
materials or one or two in combination
- Super Absorbent Polymers (SAP) (60-300 mm size) - Sodium salts of
poly-acrylic acid, polyacrylamide copol., ethylene maleic anhydride copol., cross-linked
carboxy- methyl-cellulose, polyvinyl alcohol copol, etc.,
- Natural
or Synthetic Light Weight Aggregate Fines, expanded shale with higher water absorption
capacity.
- Coarse aggregate of nominal maximum size and gradation
- Shrinkage Reducing Admixture - SRA polyethylene-glycol.
- Saturated Wood powder / fibres
Super Absorbent Polymers (SAP) - Process
of water evaporation from within and also through the surface of concrete can be
reduced using some specific water-soluble polymers added during mixing of concrete,
which can also improve water retention in ordinary Portland cement matrix. Various
types of polymers are used in the construction industry depending on the requirement
of the properties in the finished application, for E.g. alteration of the initial
setting time (delaying setting time or rapid setting time), increased tensile adhesion
strength, higher pot life or alteration of compressive strength among others, which
can be introduced with different polymer composition. These polymers, depending
on the chemistry can be water soluble polymers or semi soluble. All water soluble
polymers are not water retentive polymers.
Polymers used as self curing chemical are cross-linked polymers, made by solution
or by suspension polymerization (cost effective) which can absorb and retain large
amount of water called Super Absorbent Polymers (SAP). They act as water reservoirs
to release water gradually, supplement the water loss and increase the water retention
of concrete compared to conventional concrete.
SAPs are a group of polymeric materials that have the ability to absorb a significant
amount of liquid from the surroundings (water uptake) through hydrogen bonding with
the water molecule and to retain the liquid within their structure without dissolving.
SAPs can be produced with water absorption of up to 5000 times their own weight.
They can be produced by either solution or suspension polymerization and the particles
may be prepared in different sizes and shapes including spherical particles.
Cross - linked Polyelectrolytes
Because of their ionic nature and interconnected structure, they can absorb large
quantities of water without dissolving. The commercially important SAPs are covalently
cross-linked polyacrylates and copolymerized polyacrylamides / polyacrylates. They
are Acrylamide/acrylic acid copolymers
Rheometer and Continuous Shear Rate Test results.
The macromolecular matrix of a SAP is a polyelectrolyte, i.e., a polymer with ionisable
groups that can dissociate in solution, leaving ions of one sign bound to the chain
and counter-ions in solution. For this reason, a high concentration of ions exists
inside the SAP leading to a water flow into the SAP due to osmosis. Another factor
contributing to increase the swelling is water solvation of hydrophilic groups present
along the polymer chain.
Mechanism of SAP swelling - Following
schematic diagram explains Mechanism of SAP swelling.
Hydrophilic water soluble polymers absorb water and keep surrounding medium moist.
The thickening effect caused by SAP can be used with advantages for some practical
situations like pumping of concrete, particularly for shotcreting of wet mix. The
yield stress and plastic viscosity of cementitious system can be studied if the
Rheometer is used to measure the rheology of concrete.
Mechanism of SAP swelling
Super Absorbent Polymers - before water absorption and after water
absorption
Collapsed Phase and Swollen phase are the two distinct states of SAPs. Repulsive
force helps in expansion of SAP and elastic free energy opposes swelling of the
SAP by a retractive force. There is a competitive balance between the repulsive
forces that act to expand the polymer network and attractive forces that act to
shrink the network which results in phase transition. Observation of SAP swelling
in concrete indicates that total absorption is about half the absorption of synthetic
fluid which in turn is several times the absorption of SAP in water.
One type of SAPs are suspension polymerized, spherical particles with an average
particle size of approximately 200 µm, where as another type of SAP is solution
polymerized and then crushed and sieved to particle sizes in the range of 125 -
250 µm. The size of the swollen SAP particles in the cement pastes and
mortars is about three times larger due to pore fluid absorption.
The swelling time depends especially on the particle size distribution of the SAP.
It is seen that more than 50% swelling occurs within the first 5 min after water
addition. The water content in SAP at reduced RH is indicated by the sorption isotherm.
Effect of time - process of Absorption
and release of Water in SAP
Dosage of SAP in concrete
Max. water absorption capacity of SAP is 1500 g/g , however commercial SAP used
in construction industry are of the capacity of the capacity of 50 - 300 g/g
, generally SAPs are added at rate of (0 - 0.6) % wt of cement. Large particles
may be broken by mixing and filling with hydration products of small SAP, as large
particles take more time for uptake of water.
Super absorbent polymer Particle - before
& after water absorption
Super absorbent polymer Particle - Different
Size as per requirement in concrete
Quantifying Effectiveness of SAP of Internal Curing Agents
Various technologies are used to study the effectiveness of using internal curing
materials, admixtures / SAP in fresh and hardened state of concrete. They are measured
experimentally using the following methods.
- Internal RH - Change internal RH with time
- Degree of hydration
- Measuring weight-loss
- Autogenous deformation
- Scanning electron microscope
(SEM)
- Compressive strength development
-
Restrained shrinkage or ring tests
- 3-D X-ray micro tomography
(Direct observation of e 3-D microstructure of cement-based materials).
-
X-Ray powder diffraction
- Thermogravimetry (TGA) measurements
- Initial surface absorption tests (ISAT)
- Water
permeability
- NMR spectroscopy
Hydration and Water transport
Water released from the SAP has function to continue hydration of cement further
in a sealed condition. The rate of change of degree of hydration depends on several
material parameters such as size and amount of SAP in the mixtures, original water
cement ratio, procedure of how the SAP is added during mixing of mortar and concrete.
source: Jensen and Hansen CCR 2001, 2002
Pore Structure (STAR 225- SAP)
Compared to normal concrete, the presence of SAP certainly changes the microstructure
of concrete. The main reasons for SAP to change the microstructure of concrete especially
the pore structure of concrete containing SAP are likely to be,
- When SAP is fully filled with water it act as a soft aggregate and
when it is empty it acts as an air void in the concrete.
- Non
uniformity of dispersion of SAP during mixing.
- The mechanism of water uptake of SAP and release of water at later
stages changes the effective w/c ratio in the early stages of hydration and water
release from SAP affects further hydration process.
- Interface between SAP and cement paste matrix may further induce
some additional pores.
Suspension-polymerized SAP
The effect of SAP on the pore structure of concrete is not only on its total porosity
but also on its pore size and pore size distribution. The increased hydration degree
of cement paste results in reduction of capillary porosity in the matrix. And also
void introduced by the SAP in the mixture is homogeneously distributed, when SAP
is distributed evenly throughout the concrete mixture.
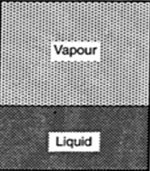 |
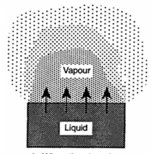 |
Closed Vapour
Transport System
|
Open Vapour
Transport System
|
Vapour Transport Mechanism (R. K. Dhir 1994)
When a pure liquid A is held in a container a certain quantity of molecules of A
will evaporate until the vapour pressure is such that the liquid and vapour phases
are in thermodynamic equilibrium. Equilibrium is achieved when the chemical potentials
(free energy) of these two phases are equal. Where as when the closed system is
opened, the vapour disperses. Continuous evaporation takes place in an attempt to
reach equilibrium.
Microstructure of concrete with SAP (R. K. Dhir 1996)
Calcium hydroxide at cement-aggregate interface in control mortar: (a) viewed side-on;
(b) viewed from above.
Calcium hydroxide at cement-aggregate interface in mortar containing 0.10M of chemical:
(a) viewed side-on; (b) viewed from above.
(a) and (b) - CSH in 28-day mortar specimen cured
in air (control).
(a) and (b) - CSH in 28-day mortar specimen cured in air
(0.10M chemical addition).
Influence of microstructure on the physical properties of Self Curing Concrete is
presented in this study. During the development of self-curing concrete it was found
that one particular self-curing admixture used produces a number of effects with
respect to particular physical properties and powder x-ray diffraction characteristics.
The paper attempts to explain these observations at a micro structural level. Two
computer models were used to illustrate the influence the admixture was thought
to have on hydrated cement microstructure. At low dosages, good strength and improved
permeability characteristics were observed. At high dosages, it appeared that the
admixture has a detrimental effect on the concrete’s compressive strength
due to an alteration of the nature of calcium hydroxide at the cement-aggregate
interface. However, it seemed that at the same dosages the CSH gel structure was
altered beneficially, producing a highly impermeable concrete. It is suggested that
although a lowering of strength does occur at high dosage, a much lower permeability
for a given strength could be obtained.
This paper concludes that there is evidence that the chemical is altering CSH gel
morphology also, possibly by growth inhibition. This appears to enhance the nature
of the CSH gel, leading to better permeability characteristics. Despite a reduction
in strength at high dosages, it can be concluded that a lower concrete permeability
for a given strength can be obtained using this chemical. The chemical dealt with
in this report has the effect of inhibiting growth of calcium hydroxide crystals.
The change in CH morphology that results can be detrimental to concrete strengths
at high admixture concentrations.
Effect of SAP on strength characteristics of concrete and mortar
Introduction of SAP in to concrete mixture results often in certain strength reduction
at early ages. Slight strength reduction is observed at the early age of few days
of curing. However the correct dosage of SAP and the internal curing water and also
optimum technological procedure of mixing casting and curing help to overcome the
strength reduction.
However some studies report that after 28 days the strength may be even exceed that
of reference concrete mixture. One of the possible reasons of the enhancement of
concrete containing SAP with age may be the improvement of degree of hydration of
cement grains, which is achieved by internal curing. In addition, cement hydration
product at later stages grow inside the original grain boundaries of SAP particles
contributing to the strength of mature system. In case of HPC, usage of SAP is mainly
to mitigate self desiccation and autogenous shrinkage without impairing the concrete
strength substantially.
In case of mortar, introduction of SAP as internal curing agent has a little influence
on the strength of high performance mortars, while the strength of cement paste
was reduced more severely. The different effect of SAP introduction in cement paste
and mortar can be explained by different largest defect size present in the solid
mortar of these materials. The tensile strength and Elastic modulus of concrete
with SAP are expected to increase as well when care is taken to mix the SAP properly
in concrete, however it does not happen always.
For Mortar
Equivalent Hydrostatic Pressure development in Mortar
Figure shows the equivalent hydrostatic pressure developed in the ASG by mortars
with different amounts of SAP type A and consequently, different amount of entrained
water. SAP additions are given by weight of cement, where o.6% corresponds to an
entrained w/c ratio of 0.075. Basic w/c ratio is 0.3 for all mixes. Temperature
is 200C.
Different Curing Conditions - There are
not many publications where different curing conditions like air curing, moisture
curing and water curing are used to compare the behaviour / properties of same mix
of concrete. Sealed curing is used for autogenous shrinkage where as air curing
or moist curing is adopted for strength studies. The table summarizes the effect
on strength of concrete with SAP addition, determined under different curing conditions
(S, M and D ) at 28 days only.
Table 1 - Effect of SAP on concrete strength at 28 days under different
curing conditions (Summary from different papers - Source -
STAR 225 - SAP)
Sl. No
|
Moist Curing (M)
|
Dry Curing(D)
|
Sealed Curing(C)
|
1
|
Compressive strength decreased by (16 - 31)%, depending on the SAP content
|
|
|
2
|
Compressive strength decreased by (28 - 35)%,
|
Compressive strength decreased by (26 - 28)%,
|
|
3
|
|
|
Compressive strength decreased by (3-22)%, Tensile strength decreased by (11-33)%,
depending on the SAP content
|
4
|
Compressive strength decreased by (8 -14)%,
|
|
|
5
|
|
|
10% reduction of compressive strength in pastes, no influence of SAP addition in
mortars
|
6
|
|
Compressive strength decreased by 2% (cubes)
13% (prisms), uniaxial strength by 19% and flexural strength by 25%
|
Compressive strength decreased by 10% (cubes)
13% (prisms), uniaxial strength by 7% and flexural strength by 31%
|
7
|
Compressive strength decreased by 30%
|
Compressive strength decreased by 20%
|
|
8
|
|
|
Compressive strength decreased by 10% (cubes)
13% (prisms), uniaxial strength by 7% and flexural strength by 31%
|
9
|
|
|
Compressive strength decreased by 36% in cubes (12-30)% in prisms, depending on
the SAP content
|
10
|
|
|
Almost no compressive strength reduction and slight increase in flexural strength
in SAP mixes Slight increase (3-4)% in compressive strength
|
Durability of Self Cured Concrete
Effect of internal curing in concrete on its durability parameters -
Dhir et al in their paper reported the results of several durability tests conducted
on self-cure concrete specimens. It was found that initial surface absorption (ISAT),
chloride ingress, carbonation, corrosion potential and freeze/thaw resistance characteristics
were all better in air cured self- cure concrete than in the air cured control concrete.
This improvement appears to be dependent on the admixture dosage, although the durability
properties obtained in the study were not as good as the film cured concrete. It
may be possible to achieve such properties with higher quantities of self-cure chemical.
Concrete that is capable of retaining greater quantities of water than ordinary
concrete when cured in air has been developed by means of addition of a self curing
chemical which was a water-soluble polymeric glycol identified as the chemical.
The water retention leads to a greater degree of cement hydration and hence improved
properties of concrete in comparison to control test specimens. One particular feature
of self-cure concrete is its good durability properties.
Shrinkage of Concrete
Volume changes in concrete due to shrinkage are main sources of Eigenstresses and
stresses due to the restraint in concrete structure that leads to many instances
of cracking. Four types of shrinkages generally considered as a result of this are
- Plastic Shrinkage occurring during first few hours after mixing
when concrete still behaves as a formable mass.
- Autogenous shrinkage
of hardening concrete as a result of hardening process.
- Drying
Shrinkage due to loss of water caused by surrounding atmosphere.
-
Carbonation shrinkage resulting from carbonation of concrete.
Autogenous shrinkage typically defined as bulk deformation of closed (sealed) isothermal
cementitious material system not subjected to external curing. Autogenous shrinkage
of normal cured concrete is slightly smaller when compared to drying shrinkage.
SAP for Mitigation of Shrinkage
Addition of SAP often in conjunction with extra water influence not only autogenous
shrinkage but also other types of volumetric changes and development of stresses
due to restrained shrinkage. Application of SAP as a means of internal curing agent
mitigates autogenous shrinkage. Advantages of SAP in concrete is that they can be
in principle engineered for special purpose of internal curing by determining the
necessary particle size and shape, water absorption capacity and other properties.
Literatures on chemical shrinkage are scanty. Due to the chemical shrinkage occurring
during cement hydration, empty pores are created within the cement paste, leading
to a reduction in its internal relative humidity and also to shrinkage which may
cause early-age cracking. This situation is intensified in HPC (compared to conventional
concrete) due to its generally higher cement content, reduced water/cement (w/ c)
ratio and the pozzolanic mineral admixtures (fly ash, silica fume). The empty pores
created during self-desiccation induce shrinkage stresses and also influence the
kinetics of cement hydration process, limiting the final degree of hydration. The
strength achieved by IC could be more than that possible under saturated curing
conditions.
Restrained and Free Autogenous Shrinkage Measurements
Figure suggested schematic effect of SAP particle size on reduction of autogenous
shrinkage. The suggested optimum size, about 100µm, refers to the swollen
state.
Effect of Particle Size on reduction in Autogenous shrinkage
Light Weight Aggregates (LWA) for Mitigation of Shrinkage
The application for the concept of internal curing by means of saturated lightweight
aggregate was studied and applied in HPC which proves to be effective in eliminating
autogenous shrinkage. High performance concretes (HPC) with extremely low water
to binder (w/b) ratios are characterized by high-cracking sensitivity, which is
a consequence of increased autogenous shrinkage. The major reason for autogenous
shrinkage - self-desiccation cannot be eliminated by traditional curing methods.
Zhutovsky et al. in their paper described an approach to optimize the size and porosity
of the lightweight aggregate to obtain effective internal curing with a minimum
content of such aggregate. In this study the primary emphasis was placed upon an
investigation of the effects of the replacement level of normal weight coarse aggregates
by saturated lightweight ones, and the degree of water saturation of lightweight
aggregate. These parameters provided the means to control the effectiveness of autogenous
curing.
Several factors affect to counteract self-desiccation and therefore, autogenous
shrinkage are (i) aggregate pore size: If it is very fine, water may not migrate
readily into the surrounding paste. (ii) The spacing between the aggregate particles:
if it is too large, the paste surrounding the aggregates may not be accessible to
the water in the aggregate within a reasonable time.
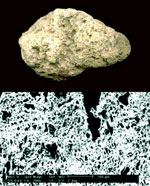 |
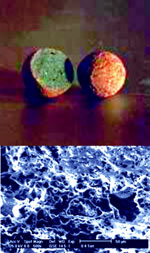 |
Crushed pumice |
Expanded shale |
Initial Surface Absorption Test (ISAT)
ISAT values obtained from concrete test specimens were compared with those of air
cured control specimens (Fig. 20). The surface of the air cured control specimens
absorbs water at a highest rate and the least permeable surfaces are those of the
time cured specimens. The higher dosage of the self-cure chemical provided a greater
improvement in surface characteristics, but at both concentrations the chemical
decreases the rate of absorption at the surface.
10 Minute Initial Surface Absorption Test Results
Literatures also summarize that the surface quality, chloride diffusion, carbonation,
corrosion potential and freeze thaw resistance of self-cure concrete provides improved
performance when compared to air cured specimens. The improvements in concrete durability
properties are dependent on dosage of SAP in it. It is conceivable that higher dosages
could produce air-cured concrete with properties rivalling those achieved in the
film-cured situation.
Measurement of RH of concrete specimen
Sorptivity Measurement of concrete specimen
Internal Curing - Merits
Internal curing can make up for some of the deficiencies of external curing,
both human related (critical period when curing is required is the first 12 to 72
hours) and hydration related (because hydration products clog the passageways needed
for the fluid curing water to travel to the cement particles thirsting for water).
Following factors establish the dynamics of water movement to the unhydrated cement
particles:
- Thirst for water by the hydrating cement particles is very intense,
- Capillary action of the pores in the concrete is very strong, and
- Water in the properly distributed particles of (fine)LWA is very
fluid.
Benefits of using SAP in concrete
SAP in concrete is advantageous, as it
- Reduces autogenous cracking resulting from autogenous shrinkage
- Protects concrete and reinforcing steel through reduced permeability
- Reduces post construction process of curing and provides higher
performance and greater durability.
- Improves rheology without
affecting Pumpability and finishability adversely
- Higher degree of finishing of structural elements and less maintenance
requirement.
- Lower turnaround time and labour requirement at
site.
- Improved rheology improves contact zone, and results in
lower maintenance,
- Greater utilization of cement and use of
higher levels of fly ash.
Potential benefits of using LWA in concrete
- Better thermal properties;
- Better fire resistance;
- Improved skid-resistance;
- Reduced autogenous shrinkage;
- Reduced chloride ion penetrability;
- Improved freezing and thawing durability;
- An improved contact zone between aggregate and cement matrix; and,
- Less micro-cracking as a result of better elastic compatibility.
First SAP
application in practice
Usage of internal curing material refers back to Roman times. Pantheon, Rome, 126
A.D. was constructed with pozzolanic cement and pumice stone for internal curing.
First SAP application was in 2006 used for the construction of Pavilion of Olympic
stadium in Kaiserslautern for FIFA World Cup (Ref: Mechtcherine et al. 2006)
Early example of internal curing - Pantheon,
Rome, 126
A.D. pozzolanic cement and pumice stone
Application Internal Curing or Self Curing materials / compounds-
From the literatures, it is clear that the internal curing is an effective means
for drastically reducing autogenous shrinkage. Internal curing is useful when ‘performance
specifications' are important than 'prescriptive specifications' for concrete. Current
application of using SAP/LWA in concrete structures have been included for shrinkage
reduction, frost protection, rheology modification, water proofing and fire protection
to name a few. Hence self curing or internal curing concept is a futuristic technology,
used for technology modifications and large applications like shortcreting, backfilling,
self compaction, low autogenous shrinkage, thin walled sections and enhanced ductility
of HPC members and for high durability.
FIFA World Cup Pavilion in Kaiserslautern( Ref:Mechtcherine et
al. 2006)
The areas of prime applications of internal curing may be concrete pavements. Precast
concrete operations, parking structures, bridges, HPC projects, and architectural
concretes. Concrete, in the 21st century needs to be more controlled by the choice
of ingredients rather than by the uncertainties of construction practices and the
weather. Instead of curing through external applications of water, concrete quality
will be engineered through the incorporation of water absorbed within the internal
curing agent. (Rajamane, N. P 2006).
Other uses SAP are in diapers, for blocking water penetration in cables, water retention
for plants, control of spill and waste fluids, artificial snow, candles, etc.,
Conclusion
Challenge of effective application of this technology lies in selection
of right type of curing agent/ absorbent / light weight aggregate fines suitable
to site conditions and type of concrete and other factors. The desired result of
internal curing can be achieved through
- Proper mix design procedure / mix proportioning technique for internal
curing (with polymer).
- Its effectiveness in tropical atmosphere condition
-
Its effectiveness for ordinary strength concrete with high w/c ratio
There are clearly many opportunities to use this technology in various functions
to improve the performance and durability of the built environment. It is expected
that future applications will increasingly move towards the use of self curing technology
in the concrete sector construction, as this technology becomes better known through
good practice and evidence of good performance records.
Until behaviour of admixtures and their effects on other properties of concrete
are readily understood, use of self curing agents remains relatively sparse. With
significant result yielding research contributions in to this area and reduction
in the cost involved in using these self curing compounds, self curing is an assured
futuristic technology which is going to gain popularity and to continue to prevail
in the industry for long.
Acknowledgment
Authors wish to acknowledge that materials are drawn from the following references
mainly from the papers of Prof. Ravindra K. Dhir, Dr. C. S. Viswanatha and Dr. Rajamane
N P along with other references.
References
- Ambily P.S, Scientist, and Rajamane N P, Self Curing Concrete An
Introduction, RILEM State of art Reports,
http://nbmcw.com
- Curing of Concrete – Cement Concrete
and Aggregate Australia, 2006.
- Dhir R K, Hewlett P C and Dyer T D, "Influence of microstructure
on the physical properties of self curing concrete, ACI material Journal, Vol 93,
No.5, 1996, pp 465-471.
- Dhir R K, Hewlett P C and Dyer T D,
"Durability of Self cure concrete, Cement and Concrete Research, Vol 25, No.6, 1995,
pp 1153-1158.
- Dhir, R. K.; Hewlett, P. C.; Lota, J. S.; and
Dyer, T. D., "Investigation into the Feasibility of Formulating ‘Self-Curing’
Concrete," Materials and Structures, V. 27, 1994, pp. 606-615.
-
Dhir, R.K. Hewlett, P.C. Dyer, T.D., "Mechanisms of water retention in cement pastes
containing a self-curing agent," Magazine of Concrete Research, Vol No 50, Issue
No 1, 1998, pp. 85-90.
- Self-curing concrete: Water retention, hydration and moisture
transportConstruction and Building Materials, Volume 21, Issue
6, June 2007, Pages 1282-1287
-
Lecture - 6B, Internal Curing, EMPA, Shrinkage and Cracking of Concrete: Mechanisms
and Impact on Durability, ETHZ, 26.10.11.
- Ravindra K. Dhir, Peter C. Hewlett, and Thomas D. Dyer , Influence
of Microstructure on the Physical Properties of Self-Curing Concrete, ACI Materials
Journal, V. 93, No. 5, September-October 1996.
- Kung-Chung Hsu and Jing-Siang Jhuang, Effect of a Hydrogel
on the self Curing Properties of Mortars.
- STAR 225 - SAP, Application of SAP in concrete Constructions, published
by Springer,
http://www.springer.com .
- Tarun R. Naik, Fethullah Canpolat,
SELF-CURING CONCRETE, Report No. CBU-2006-11 REP-610, April 2006, A CBU Report.
- Viswanatha C S. ‘Self Curing Concrete - Recent Developments,
Proceedings of National Seminar on Engineered Concrete, 2008.
-
Chella Gifta C., Prabavathy S. and Yuvaraj Kumar G. Study on internal curing of
High Performance concrete using super absorbent polymers and light weight aggregates,
Asian journal of Civil Engineering. Vol.No.. 14, NO. 5 (2013) pp. 773-781
Authors
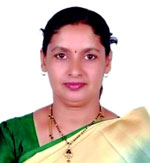 |
Bharathi Ganesh is an Associate Professor
in the Department of Civil Engineering, Global Academy of Technology, Bangalore,
and Karnataka, India. She has 2 years of industrial experience and nearly 20 years
of Teaching experience. Her research interest includes Self Compacting Concrete,
Fresh and Hardened Properties of Concrete, Fly Ash and Pond Ash in Concrete. She
is a Life Member of profession bodies ICI, ACCE, INSDAG, IASE, IWSF and INSTRUCT.
|
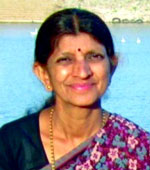 |
Dr. H. Sharada Bai is a Professor in the
Department Civil Engineering, UVCE, Bangalore University, Bangalore, India. She
has more than 30 years of Teaching Experience and is also a Design and Proof Checking
Consultant. Her areas of interest include self compacting concrete, use of alternative
materials in concrete, analysis and Design of Structures, and evaluation of structural
systems. She is a Life Member of profession bodies- ICI, ACCE, INSDAG, and ISTE.
|