Steel Fiber Reinforced Self Compacting Fly Ash Concrete
M. C. Nataraja
Professor, Department of Civil Engineering, Sri Jayachamarajendra College of Engineering,
Mysore - 570 006, India, (nataraja96@yahoo.com)
Abstract
Presently Self Compacting Concrete (SCC) is of great interest and has gained wide use especially in the case of difficult casting conditions such as heavily reinforced sections. From a rheological point of view, the use of a Viscosity Modifying Admixture (VMA) along with adequate Hyper Plasticizer (HP) enables to ensure high deformability and stability of SCC. The behavior of SCC as a structural material can be further improved by adding adequate steel fiber reinforcement. In fact, the fibers can convert the brittle behavior of SCC into a pseudo-ductile behavior up to a crack width that is acceptable in the design. In this paper flow characteristics and compressive strength of self compacting fly ash concrete with and without steel fiber are discussed.
Keywords: Self- compacting concrete, Fly Ash, Steel fibers, Compressive strength, Flow characteristics.
1.Introduction
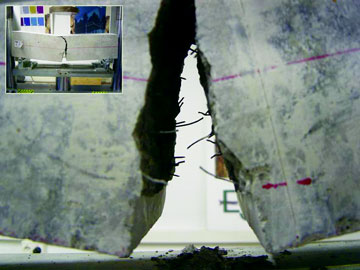 |
SCC is a highly fluid concrete that does not require any vibration during the placement process. Thus, this kind of concrete is of great interest with regard to the economical, technical and environmental points of view [1–3]. Although SCC can be used in most construction sites, its rheological characterisation must be improved to control its placement. Fresh SCC must be stable to ensure its homogeneity and adequate mechanical strength. However, several problems like bleeding, settlement or segregation can occur simultaneously on construction sites. Segregation can appear during placing (referred to as “dynamic segregation”) or afterwards, during the dormant stage (referred to as “static segregation”). “Static segregation” consists of the sedimentation of the coarsest aggregates of the suspension under gravity forces. Several empirical tests are proposed to estimate the segregation risk of SCC [4]. More knowledge is needed for better understanding of segregation and to improve existing tests. In this paper, SCC is produced using fly ash and steel fibers and are tested for flow and strength properties.
2. Literature review
This new type of concrete, which can be compacted into every corner of a formwork purely by means of its own weight, was first proposed by Okamura [5]. In 1986, he started a research project on the flowing ability and workability of this special type of concrete, later called SCC. The self-compactability of this concrete can be largely affected by the characteristics of materials and the mix proportions. In his study, Okamura has fixed the coarse aggregate content to 50% of the solid volume and the fine aggregate content to 40% of the mortar volume, so that self-compactability could be achieved easily by adjusting the water to cement ratio and superplasticizer dosage only. Other researchers in Japan started to investigate SCC to improve its characteristics. Ozawa [6] completed the first prototype of SCC using locally available materials. Khayat et al [7] found out that the use of self-consolidating concrete can facilitate the placement of concrete in congested members and in restricted areas. According to study made by Liberato Ferrara [8], fibre-reinforced SCC can be produced for precast building components, incorporating either metal fibres or polymeric synthetic slipping fibres or a combination of both. Boel et al [9] found out that the durability of SCC is greatly influenced by its permeability for potentially aggressive application. As the pore structure of SCC might be different in comparison with traditional concrete (TC), some changes in durability behaviour may occur. According to Persson [10] fire resistance of SCC was better than that of TC. Stefan Kordts et al [11] observed that when SCC is used, it is important that the concrete has all the requisite fresh concrete properties at the time of placement. Lots of research is being carried by Indian investigators as well.
3. Materials
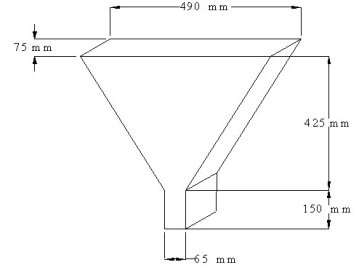 |
Fig.2 V-Funnel Test Equipment (Rectangular Section) |
Fig. 3 Steel Fibers Type Used
Following materials are used in the present study. 43 Grade OPC confirming to IS-8112 (1989) [12]. Locally available river sand confirming to Zone II having specific gravity (SSD) 2.59 and fineness modulus 2.45. Coarse aggregate passing 12.5 mm and retained on 4.75 mm sieve. Tap water for mixing and curing. Glenium 51 HP and Glenium stream 2 VMA. Class F flyash having specific gravity (SSD) 2.18. Crimped steel fibers having 0.8 mm diameter and aspect ratio of 55.
4. Mix Proportion of SCC
The mix composition as per Table 1 is chosen by trial and error so as to satisfy all performance criteria for the concrete in both the fresh and hardened states.
*Cm-Cementitious materials, F = Crimped steel fibers, FA = Fly ash
Label
|
Ingredients
|
|
C
(Kg)
|
FLY
ASH
(Kg)
|
FA
(Kg)
|
CA
(Kg)
|
Water
( l )
|
W/Cm*
|
HP
(% by weight of cement)
|
VMA
(% by weight of cement)
|
Fibers
(% by weight of concrete)
|
HP-VMA
|
600
|
---
|
900
|
650
|
216
|
0.36
|
3
|
1.5
|
---
|
HP-VMA-0.5%F
|
600
|
---
|
900
|
650
|
216
|
0.36
|
3
|
1.5
|
39
|
20% FA
|
480
|
120
|
900
|
650
|
216
|
0.32
|
3
|
1.5
|
---
|
20% FA-0.5%F
|
480
|
120
|
900
|
650
|
216
|
0.32
|
3
|
1.5
|
39
|
40% FA
|
360
|
240
|
900
|
650
|
216
|
0.30
|
3
|
1.5
|
---
|
40% FA-0.5%F
|
360
|
240
|
900
|
650
|
216
|
0.30
|
3
|
1.5
|
39
|
5. Experimental Procedure
5.1 Slump Flow Test and T50cm Test
The slump flow test (Fig. 1) is used to assess the horizontal free flow of SCC in the absence of obstructions. The diameter of the spread concrete circle is a measure of filling ability of the concrete. Higher the slump flow value, greater is its ability to fill formwork under its own weight. The T50 time is a secondary indication of flow. Lower time indicates greater flowability.
Definition of ?p/m : ?p/m = (d/d0)2 – 1, Where, d = ½ (d1 + d2)
5.2 V Funnel Test and V Funnel Test at T5minutes
The V-funnel test (Fig. 2) is used to determine the filling ability (flowability) of SCC. The funnel is filled with about 12 liter of concrete and the time taken for it to flow through the opening is measured. After this the funnel can be refilled with SCC and left for 5 minutes to settle. If the concrete shows segregation then the flow time will increase significantly.
For SCC a flow time of 10 seconds is considered appropriate. The inverted cone shape restricts flow and prolonged flow times may give some indication of the susceptibility of the mix to blocking. After 5 minutes of settling, segregation of concrete will show a less continuous flow with an increase in flow time. The type of fiber, its addition to concrete, the nature of flow and its characteristics can be seen in Figs. 3 to 7.
6. Flow Characteristics for SCC
The results pertaining to the variation in flow of SCC incorporated with different percentages of Fly Ash (FA) are as shown in Table 2. Slump flow test is a better measure than V funnel test for fiber reinforced SCC.
7. Hardened properties
The density and compressive strength at 7 and 28 days are determined as per IS: 516 - 1975 and the results are represented in Tables 3 and 4.
Table 3 Compressive strength of concrete cubes (150 mm Size)
Label
|
Strength (MPa)
|
Without Fibers
|
With Fibers
|
7 days
|
28 days
|
7 days
|
28 days
|
HP-VMA (Control)
|
46.65
|
56.86
|
47.55
|
56.78
|
20% FA
|
42.03
|
57.81
|
41.02
|
57.88
|
40% FA
|
39.10
|
55.40
|
37.68
|
54.32
|
Table 4 Density of concrete cubes (150 mm Size)
Label
|
Density (Kg/m3)
|
Without Fibers
|
With Fibers
|
7 days
|
28 days
|
7 days
|
28 days
|
HP-VMA (Control)
|
2383
|
2399
|
2372
|
2375
|
20% FA
|
2376
|
2360
|
2365
|
2351
|
40% FA
|
2343
|
2350
|
2355
|
2349
|
8. Discussion
8.1 Flow Characteristics for SCC
Table 2 represents flow characteristics of SCC with different mix proportion. The test was carried out with different w/cm so as to obtain constant slump flow. The slump flow value however decreased with the introduction of fibers because of the resistance posed by the fibers for the flow. The V- funnel test was conducted for different mixes without fibers but the test was not successful for mixes containing fibers due to its blockage.
8.2 Compressive Strength of SCC
Table 3 and 4 represents hardened properties of SCC with and without fibres. The compressive strength of control SCC is about 55.40MPa. With the addition of 0.5% fibers, the compressive strength has increased marginally. However the flow has decreased. With the addition of FA (20% and 40%), the flow has increased substantially. In order to maintain a constant flow of about, the water content has been reduced. With this the effective water to cementitious ratio decreased and hence substantial increase in compressive strength. On the other hand due to the addition of FA, the compressive strength has decreased (as observed in SCM) due to poor pozzolanic activity of flyash at that age. In spite of this, the compressive strength of SCC with FA is equal to or slightly in excess of that of control SCC mix. With this there exists considerable advantage of using FA in concrete without compromising compressive strength and flow requirements. However, due to the addition of steel fibers, the compressive strength of concrete is not affected much.
9. Conclusions
Following are the few conclusions drawn based on the limited study conducted.
1. The workability of SCC with FA can be easily evaluated by combining slump flow and V- funnel tests.
2. The effect of FA on fresh concrete is to improve the flow characteristics of fresh concrete.
3. For producing self compacting concrete high amount of fines, hyperplasticiser and viscosity modifying admixtures are required.
4. Good mixing and quality control are required to get good SCC.
5. Flow and time so determined are the two important properties of SCC to know its performances.
References
- H. Okamura, M. Ouchi, "Self compacting concrete. Development, present use and future", in: A. Skarendahl, O. Petersson (Eds.), Self compacting concrete, Proceedings of the first International RILEM Symposium, RILEM Publications, La Ferte´-Mace´ (France), 1999, pp. 3 – 14.
- A. Skarendahl, "The present–the future of SCC", in: O. Wallevik, I. Nielson (Eds.), Self compacting concrete Proceedings of the third International RILEM Symposium, RILEM Publications, 2003, pp. 6– 14.
- J. Walraven, "Structural aspects of self compacting concrete", in: O. Wallevik, I. Nielson (Eds.), Self compacting concrete, Proceedings of the third International RILEM Symposium, RILEM Publications, 2003, pp. 15-22.
- F. Cussigh, M. Sonebi, G. De Schutter, "Project testing SCC segregation test methods", in: O. Wallevik, I. Nielson (Eds.), Self compacting concrete, Proceedings of the third International RILEM Symposium, RILEM Publications, 2003, pp. 311 - 322.
- H. Okamura and Masahiro Ouchi, (2003), "Self - compacting concrete, Development, present use and future", Journal of Advanced Concrete Technology, Vol. 1, No. 1, pp. 5-15.
- K. Ozawa, N. Sakata and H. Okamura (1995), "Evaluation of self compactability of fresh concrete using funnel test", Concrete Library of JSCE, Vol. 25, pp. 59-80.
- K. H. Khayat, C. Hu and H. Monty, "Stability of Self-compacting concrete, advantages and potential applications", H. Okamura and M. Ouchi (eds), Self-compacting concrete proceedings of the First International RILEM symposium, Stockholm, RILEM publications, pp. 143-152, 1999.
- Liberato Ferrara and Alberto Meda, "Relationships between fiber distribution, workability and the mechanical properties of SFRC applied to precast roof elements", Materials and Structures, Vol. 39, pp. 411-420, 2006.
- V. Boel, K. Audenaert, G. De Schutter, G. Heirman, L. Vandewalle, B. Desmet, and Vantomme, "Transport properties of self compacting concrete with limestone filler and fly ash", Cement and Concrete Research, 2001.
- Bertil Persson, "Fire resistance of Self-compacting concrete", Materials and Structures, Vol. 37, pp. 575-58, 2004.
- Stefan Kordts, Wolfgang Breit and Dusseldorf, "Assessment of the fresh concrete properties of Self- compacting concrete", In the Journal Beton, pp. 113-123.
- IS: 8112-1976, "Specification for 43 Grade Ordinary Portland Cement", BIS, New Delhi.
- IS: 2386(PT2)-1963, "Methods of test for aggregates for concrete, Part 1 Particle size and shape".
- EFNARC, specification and guidelines for self-compacting concrete. European Federation for Specialist Construction Chemicals and Concrete Systems, Norfolk, UK, English ed., February 2002.
Author
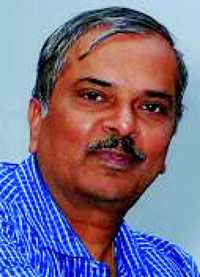 |
M C Nataraja
Professor, Department of Civil
Engineering, Sri Jayachamarajendra
College of Enginering, Mysore.
|