Improved Tunnel Fire Protection
A research team at Ruhr-University Bochum in Germany has developed a method of spraying steel-fibre-infused shotcrete onto the surface of tunnels, greatly enhancing the ability to withstand high-intensity fires, explosive blasts, or a combination of the two. The method shows promise in bolstering the security performance of critical infrastructure.
The research team is led by Goetz Vollmann, Ph.D., Dr.-Ing., an assistant professor at the university's Institute for Tunnelling and Construction Management. The project, funded by the German Federal Ministry for Education and Research, began as an examination of the security of critical bridges and tunnels with a focus on finding ways to enhance that security. "We took an all-hazard approach and naturally fire and explosion—and especially a combination of both—are the most severe threats, especially for tunnels," said Vollmann, who provided written answers to questions posed by Civil Engineering online.
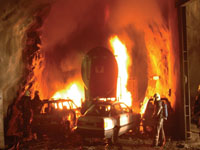 |
The researchers found that although there are several methods available for increasing the resiliency of concrete or steel infrastructure, most are so highly specialized they focus either on fire or blast resiliency, bolstering one quality at the expense of the other. "For instance, high-performance concrete, whose strong matrix has a positive effect in terms of explosion, might be too brittle in a fire threat scenario, leading to increase spalling," Vollmann explained.
|
"[And,] most of the products can only bmanufactured as prefabricated boards due to their complicated manufacturing principles." The team focused on shotcrete because it can be applied to a variety of surface shapes and materials, and is especially well-suited to tunnel applications. From earlier research, the team knew that shotcrete with many embedded steel fibers and a smaller amount of synthetic fibers would provide the compressive strength they wanted to achieve.
"The problem was naturally the workability of the shotcrete with the needed levels of steel and PP [polypropene] fibers," Vollmann said. The team was attempting to use 140 kg/m 3 of steel fibers and another 3 kg/m 3 of PP fibers, when the conventionally accepted limit is closer to 70 kg/m 3 . Additionally, the team focused on ultrahigh-performance concrete, which is much stiffer than typical shotcrete.
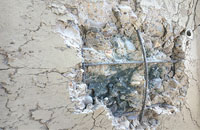 |
"For months we struggled with the workability of the wet mix. As expected, the high amounts of fibers ... together with the basic mix design made the concrete stiff and not workable at all, at least not for the application that we had in mind," Vollmann said. To solve the workability issue, the team experimented with adding high levels of air-entraining chemicals to the concrete mixture. |
A traditional concrete slab shows extensive damage from blast testing and retains just 20 percent of its original bearing capacity. © Goetz
Vollmann/Fraunhofer Ernst-Mach-Institute.
Although air entrainment is common in the concrete industry and is often used to bolster performance in applications that will be exposed to freeze-thaw cycles, the team went far beyond the typical levels for this application. "For our test series, we simply ignored the normal levels of air in a concrete mixture and instead tried to go to extremes, looking at how much air we could add and how the mixture would react," Vollmann said. The team found they could exceed 20 percent air by volume and still have a stable mixture.The air bubbles function as ball bearings,releasing the fibers to move more freely within the shotcrete and enabling the team to spray the mixture more effectively.
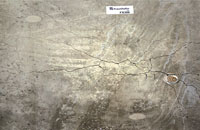 |
A concrete slab covered in a layer of shotcrete that was embedded with steel fibers withstood blast testing conducted at the Fraunhofer Ernst-Mach-Institute in Freiburg, Germany, much better than the traditional slab, maintaining 60 percent of its bearing capacity. © Goetz Vollmann/Fraunhofer Ernst-Mach-Institute |
The shotcrete is applied via a high-pressure nozzle at speeds of 50 to 80 km per hour, forming layers as much as 35 cm thick. An accelerating agent is added to the mixture as it emerges from the nozzle to enable the application of thick layers and to increase the shotcrete's early compressive strength.
A defoaming agent is also added at the nozzle. "The aim is to extract the previously added air on the concrete's way from the nozzle to its application target," Vollmann said.In early testing conducted at the Fraunhofer Ernst-Mach-Institute in Freiburg, Germany, the mixture greatly enhanced blast protection. A coated slab exposed to a blast retained 60 percent of its bearing capacity, compared to just 20 percent for an untreated slab. Fire performance also improved.
The slab showed no spalling when exposed to fire that reached 1,200°C within 5 minutes, burned feely for 55 minutes, and then endured a long cool down phase. The shotcrete is still in the prototype stage; the research team and its industrial partner, MC-Bauchemie—a chemical manufacturer headquartered in Bottrop,
The air bubbles function as ball bearings, releasing the fibers to move more freely within the shotcrete and enabling the team to spray the mixture more effectively.
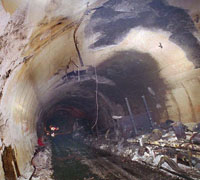
|
Germany—are working on additional refinements to the mixture and its workability. "We are still not sure that we have reached the limit state of fibre content or workability," Vollmann said. "We also envision that there are other applications of a fibre concrete with huge amounts of fibres, where you don't need these enormous contents, but still more than you would normally expect." Bridge repairs are one such area, he said. "We are already formulating new proposals for additional research."
|