NEW SCIENCE MUSEUM, MIAMI
New Science Museum at Miami seems hell bent on making the construction process as interesting as possible. The shape is crazy and looks like martini glass. It took 25 hours of continuous, hyper-precise pouring to finish the job.
Soaring upwards from Biscayne Bay, MiaSci will share the city's 40-acre Museum Park with the new Miami Art Museum, creating a powerful cultural magnet in downtown Miami. In this vibrant New City Park, MiaSci will enjoy a waterfront setting amid public gardens, fountains, pools and natural Florida landscaping. Visitors to MiaSci will be able to stroll down to the bay, relax in the garden or enjoy outdoor games in an inviting South Florida setting.
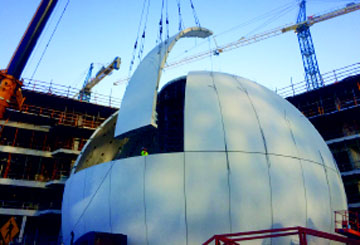
|
A key attraction in the city's open-air waterfront Museum Park, MiaSci will be located east of Biscayne Boulevard, south of I-395 between the new Adrienne Arsht Center for the Performing Arts and the American Airlines Arena in downtown Miami. Museum Park is easily accessible via the downtown Miami Metromover system, which connects with the countywide Metrorail and Metrobus transit systems. In addition, Museum Park will have extensive underground parking to accommodate museum visitors. Unlike most planetariums, which are constructed inside an existing building that serves as a structural framework, the museum's concrete orb will support itself which made constructing it a logistical challenge. Think of it as re-assembling an orange that you've already peeled. The main structure of the orb is made up of 32 concave pieces of concrete, each of which weighs 23,000kg. First, the team at Skanska had to set up the orange's fake "core", a metal tower that would serve as the stabilising element as the skin was put into place. Then, the company explains, each massive section was lifted carefully into place by a 500-tonne hydraulic crane.
But the real kicker was that crews had to work around the clock seamless day and night shifts over the course of more than two weeks to finish the job. "The team erected panels during the day and welded the panels at night so they could be ready to erect new panels in morning and maintain schedule," says Skanska. Let's just hope some of the people attending midnight Pink Floyd light shows in this thing will appreciate the round-the-clock work that went into building it.
Designed to provide a welcoming environment in keeping with South Florida's unique subtropical climate, MiaSci incorporates advanced communications and energy-conservation technology, as well as a host of visitor-friendly features. Structured around a lushly landscaped indoor and outdoor 'living core' of terrestrial and aquatic exhibits, featuring one-of-a-kind aquarium components, a state-of-the-art digital dome, hands-on exhibits and interactive digital technology, MiaSci will offer one of the world's most exciting museum experiences. Every aspect of the three-story, 250,000-square-foot MiaSci building is designed to inspire the mind, engage the senses and stimulate the imagination.
Dubai leads the world in sustainable construction with green cement
Landlords and contractors must now use green cement for the construction of new buildings in Dubai as part of a strategy to protect the environment and reduce gas emissions. New legislation forcing all landlords, contractors and consultancy companies to use the environment-friendly substance will be enforced on April 1, Dubai Municipality Director Hussein Lootah has been quoted as saying.
He said the decision is intended to protect the environment by reducing emissions of carbon dioxide and other toxic gases. "The municipality will inspect new construction sites and check the cement used in buildings after the decision is enforced. Using green cement will be a pre-requisite for granting construction permission," he said.
Another municipal official said companies failing to abide by the new decision will be stopped and penalised. "Besides depriving them from construction permission, violating companies will be fined," said Ahmed Al Badwawi, studies director at the municipality.
Green cement, which was developed in Germany nearly three years ago, is material that meets or exceeds the functional performance capabilities of ordinary Portland cement by incorporating and optimising recycled materials, thereby reducing consumption of natural raw materials, water, and energy, resulting in a more sustainable construction material.
Read more at http://www.constructionglobal.com
One Twisted RC Wall Building
A layer of glass envelopes this pair of homes in Zurich, while a zigzagging concrete partition between them is the only opaque wall in the building. Named House with One Wall, the concrete and glass building was designed by Swiss architect Christian Kerez for a plot in Witikon, east of the city. Perched on a slope, it offers residents views of nearby Lake Zurich.
The building features an elongated hexagonal floor plan, and all six of its elevations are wrapped in glazing. Inside, a zigzagging concrete wall divides the structure in half to create semi-detached homes for two families. Kerez purposely conceived this concrete partition as the building's only opaque wall, lending the house its name.
"The dividing wall is the only wall in the entire house," explained the architect, who completed the project in 2007. "It cannot be crossed anywhere." "It is the load-bearing structure and the installation core, its folds define all of the rooms and it determines how the view from the entirely glazed building is divided between the two living units," he added.
The course of the concrete wall changes from floor to floor, providing a variety of nooks and recesses on either side for kitchens, bathrooms and storage spaces. This arrangement allows service areas to be neatly tucked into the wall, leaving living spaces uncluttered. The shape of the wall is reversed on each side, producing variations between the two residences - a concave space on one side corresponds with a protrusion on the other, widening and narrowing the floor plan at different points.
"The wall between the two units has folds in it so that it will not fall over, like folding a piece of paper so that it can stand on end," said Kerez, explaining how he devised the wall as both a separating and structural element. "The folds are different from floor to floor. One room is concave, another convex. One room is open plan, another has sections."
Only the bathroom in each property is completely enclosed. There are no further partition walls and each floor consists of one long, open-plan room designed to take advantage of the views. Concrete slabs are left exposed across the ceilings, floors and walls to create a pared-back aesthetic. The glass walls are interrupted only by slim white frames and drapes can be pulled along the glazing to provide varying degrees of privacy. A tall enclosure surrounds the sloping plot, concealing the ground floor of each home and providing a small first floor garden on top of its walls. Two doors in the wall lead from the pavement into the two halves of the house. Concrete staircases connect to the first-floor living area of each home, where glass doors slide back to provide access to the garden on top of the perimeter wall.
Project credits:
Architect: Christian Kerez
Project team: Jürg Keller, Andreas Skambas, Fumiko Takahama, Ute Burdelski, Ryuichi Inamochi
Structural engineer: Dr. Schwartz Consulting AG, Zug, Joseph Schwartz
Facade: Krapf AG, St-Gallen
Construction management: BGS, Rapperswil
To read more: http://www.dezeen.com/2015/03/30
Future Buildings with Self-Repairing concrete
Bridges, tunnels and other civil engineering structures could become safer thanks to self-repairing being developed as part of a European research project. Engineers at Ghent University in Belgium have taken a lead role in the pioneering work. One of the team, Elke Gruyaert, explained the process:
"The concrete is filled with super-absorbent polymers. So when a crack appears, water comes in, and the super-absorbent polymers swell and they block the crack from further intake of water." The polymers are added to the concrete mix. Once it is dry, the researchers crack it to see how it reacts. Then they quantify its mechanical behaviour, impermeability and durability.
Brenda Debbaut, an industrial engineer at Ghent University, says the results are very quickly evident: "If a small crack starts healing immediately, then there is no risk that it grows bigger. So the total structure won't run the risk of falling down. We want to stop the problem before it is big enough".
Scientists working on the European-backed research project think these elastic polymers can indeed protect structures bearing dynamic and mechanical loads. In bridges and tunnels even tiny cracks turn into potentially dangerous damage.
Nele de Belie, Technical Director of the Magnel Laboratory for Concrete Research says impermeability is the key factor: "You do not have healed concrete regain its strength completely. It's strong enough as it is. What you do want to regain is the liquid tightness and impermeability, so that durability still remains fine".
There are other biological products that can be used to help concrete repair itself. At Delft University of Technology in the Netherlands, researchers have identified another agent to help concrete self-heal bacteria.
"These are bacteria that we have isolated from locations in our planet that have conditions which are similar to concrete," says Henk Jonkers, a biologist at Delft University of Technology. "One condition is rock-like. The other condition is being very alkaline, so very high PH conditions. These bacteria like to grow under those conditions. These bacteria are not pathogenic, and are not harmful for human beings or for the environment".
As soon as a small crack appears, bacteria contained within the concrete mixes with leaked water, creating calcium carbonate that seals the crack. Researchers are currently testing how impermeable the bacteria-driven sealing really is.
Read more@ http://www.euronews.com/2015/03/30/building
New Skins for Leaky buildings
In the Italian city of Milan a major European research project is examining the energy efficiency of new insulation materials. It aims to assess the advantages and disadvantages of these materials, and establish how and where they can be used.
Around half Europe's buildings were built before 1975. Some have architectural value, others less so, but many hide an ugly reality, as Emilio Pizzi, an architectural engineer at the Politecnico di Milano University, explained: "These buildings were built in a time when energy parameters like efficiency, consumption and emissions were not a top priority. So there's a strong need to transform and update the thermal performances of Europe's architectural heritage."
"It's time to innovate new systems, to retrofit these buildings with energy efficiency in mind," he added. The researchers have developed new insulation materials to make old buildings more energy efficient, in terms of their facades, wall cavities and interiors.
Karim Ghazi Wakili, a physicist with EMPA Research Institute, showed euronews three prototypes: "[The first} is insulation material made mainly out of three layers of polyester fibers. They are supposed to have the highest thermal insulation.
"The next material has only one layer of polyester fibers. And it has two textiles on both sides. "And the third material is the cheapest one. It is made out of a material called 'perlite'. It is thicker because perlite has higher thermal conductivity."
Researchers have tested these materials in a building of the Politecnico de Milano University in Italy. It was built in 1965. The inner walls of one room were covered with sensors and fitted with the three prototypes of insulation materials.
"The sensors measure temperature, humidity and heat flow at three different places; outside the building - that's why we have sensors installed on the facade - in the cavity walls, and finally on the inner surface of the walls," explained Gabriele Masera, a building engineer at Politecnico di Milano University.
"Outside sensors also measure radiation and wind speed. This way we are able to see how much heat leaks from the different materials in building. All the data will help us build a mathematical model that will allow us to understand how each material reacts to different climatic conditions." Magnetti Building in Milan, which makes re-fabricated kits for retrofitting exterior facades, is the kind of company the research is aimed at.
Read More@ http://www.euronews.com/2014/09/08/new-skins
Poro-elastic Road Surface
The PERSUADE project is testing the poro-elastic road surface on trafficked roads. This EU funded project aims at developing the experimental concept of a poro-elastic road surfacing (PERS) into a feasible noise-abating measure as an alternative to, for example, noise barriers. Early PERS test tracks in Japan and Sweden have demonstrated that extreme noise reductions can be achieved (up to 12 dB (A)) in comparison with conventional dense asphalt concrete or SMA pavements. Expensive and intrusive noise barriers would hence become redundant in many cases.
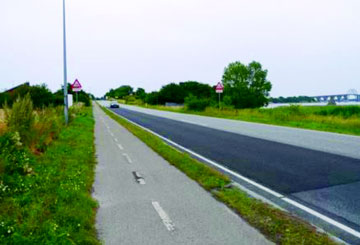
|
The specific feature of this new type of road surfacing, invented in Sweden in the late 1970's, is that it consists mainly of rubber granules from recycled car tyres, bound with a synthetic resin, such as polyurethane. It may also contain mineral material (stone aggregates) and chemical additives to enhance durability and skid resistance, as tried out in Japan and Sweden in previous projects. It contains no bitumen. So far, its inadequate durability has been the major barrier for its use as a noise abatement measure, and this is still the case.
PERSUADE has been scheduled for a duration of six years and an overall budget of 4.5 million €. Twelve partners from seven European countries are cooperating in this project, including research institutes, universities and companies representing the sectors of industry involved.
In the first half of the project, two promising mixes have been developed in the laboratory. This phase has been followed by testing of the mixtures on small scale "pilot" test tracks (typically 10 - 50 m²) A first full scale test track was built in Kalvehave, Denmark in June 2013, with a length of 75 m, a width of 3,5 m and a thickness of 4 cm, but this test track was replaced in June 2014 by a test track using an improved mix. In August-September 2014 four more full scale test tracks have been built in Belgium, Sweden (two) and Poland, with a length varying between 24 m up to 75 m. These consist of partly different mixes, are constructed in different ways and are laid on roads carrying different traffic volumes. The test tracks look very nice so far and the noise reduction compared to conventional asphalt pavements is remarkable (in one case 11 dB). An intensive monitoring program has been started on each of the test tracks in order to extract as much information as possible from them regarding a variety of relevant parameters: noise reduction, durability, skid resistance, rolling resistance, winter performance, etc.
Read more@ http://persuade.fehrl.org/
How to Keep From Blowing Construction Bids
Blowing a bid has got to be about the most frustrating error a contractor can make. Frankly there is no decent excuse for majorly blowing a bid. Your estimating must be solid. If your estimator blows a bid that means he succumbed to one or more highly avoidable mistakes including overlooking scope, not analyzing historical job cost data and failing to account for all the costs of the project.
Estimating must be based on the reality of your crew's field performance. Far too frequently estimators assume they know the time and cost it takes to perform work without ever having systematically analyzed the historical job cost data. Estimator after estimator develops elaborate estimating systems loaded with production data that has never been verified to be accurate. They commonly use numbers that have been met once in the past under ideal conditions. They assume that since the production crew hit those numbers once they should be able to hit them every time (they have no concept of random variation and how it drives ups and downs in performance).
It really is quite sad how few contractors know their cost of work. Few know how to design and deploy a proper job costing system. Fewer still know how to analyze and correctly interpret the data they collect. It is so rare that those contractors who job cost well almost always possess a strong competitive advantage over their competition. They know which jobs to price aggressively and which ones to avoid.
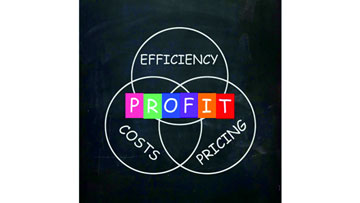 |
Another common estimating mistake is rushing through the takeoff. Estimators must have sufficient time to make and generate accurate takeoffs. Construction drawings and specifications are notoriously inconsistent. Some designers put all of the requirements on the drawings. Some bury many of their requirements in the specifications. Often a critical note is placed on a drawing many sheets away from the norm. The details can be cryptic and difficult to figure out. Digging through all of those documents takes a ton of time. Instead of letting your estimator rush through a takeoff it is far better to cut the number of takeoffs you are processing by a third or more in order to ensure your estimator moves slowly enough to not over-look scope. By far, more bids are blown by overlooking scope than by being overly optimistic on production rates.
A third common estimating error is failing to properly account for all of the costs of the project. Properly allocating for big equipment is the central contributor to this problem. Another common costing error is overlooking overtime or off-shift work that is required to meet the construction schedule. Both lead to a gross underestimation of the required wage rates.
Another important step is to hold your estimators accountable for the quality of the work they do. Will you jump down the throat of your estimator as fast as you will jump down the throat of your foremen? You should.
If your company relies on salesmen for accurate takeoffs and estimating, good luck with that. Salesmen sell. Estimators predict construction costs. Salesmen need to excel at persuasion. Estimators need to excel at accuracy. The two skills are almost diametrically opposed (right brain versus left brain). Don't expect salesmen to estimate well, and don't expect estimators to sell well.
If you do blow a bid, run the numbers for walking away. It often is much better to walk away than to proceed with the job and hope you'll recover enough to break even - even when a bid bond is involved. For an example, I met an excavator that lost over half a million dollars on a job he could have walked away from for $60,000. I asked him at what point did he realize his estimator had blown the bid, and he told me it was when the prices were revealed. I asked him why he didn't walk away from the project, and he told me he didn't want to sacrifice his bid bond. He knew his price was $400,000 low yet couldn't bring him to sacrifice $60,000. His story is too common.
Read More@ http://www.forconstructionpros.com/article/12060319
Five solutions that can bring significant energy savings
1. Reflective Indoor Coatings
By reflecting light better than normal paints, these coatings maximize the feeling of space and illumination. This in turn allows reducing the amount of energy used for artificial lighting and/or increases the perceived illumination by natural light. These coatings optimize the use of natural and artificial lighting (increased perceived light up 20%, or 20% energy reduction for the same light perception) and can help keep sunshine radiation heat inside the building in wintertime. In recent tests, reflective indoor coatings have shown a life expectancy of 5-10 years without losing any performance. The cost of these coatings is only marginally higher than that of 'normal' good quality paints. The effect of using these coatings is highest in climate zones which suffer from limited daylight intensity and duration (North and middle Europe).
2. High reflectance and durable outdoor coatings
These coatings reflect sunlight radiation both in the visible and infrared parts of the spectrum. When applied to roofs and walls, the reflection of the sun's energy reduces roof and wall temperature and as a consequence also reduces the heating of spaces underneath the roof and inside the walls. High reflectance and durable outdoor coatings applicable on building roofs and walls in hotter climate regions can save up to 15% of air conditioning energy consumption while also allowing for down scaling the size of the air conditioning system. Life expectancy of this technology is 12-15 years depending on the climate. Costs of applying these coatings are affordable and offer reasonable payback times. In case a roof needs re-painting anyway for maintenance reasons, then choosing a high quality, low LCA solar reflecting paint is an obvious smart choice especially in sunny, Southern European cities.
3. Phase Change Materials
PCM are available on the market as an active ingredient of a range of semi-finished materials: plaster, cement, plasterboard and multifunctional wall and roof modules. When used in (interior) walls and/or ceilings, the PCM enables such walls and ceilings to absorb and store excessive heat during the day, in order to dissipate that excessive heat during the night when air temperatures have gone down. PCM basically increase the thermal inertia of the wall and ceilings, making them behave like the old-fashioned thick stone walls found in buildings of hundreds of years ago. As such, PCM containing walls and ceilings reduce fluctuations of the inside temperature.
In recent tests, PCM has demonstrated to have a life expectancy of 30 years without losing any performance. In concrete cases, it has been shown that up to 10% of cooling energy can be saved. In addition the PCM allows downsizing of the air conditioning (AC) system which reduces the investment required for this AC system.
4. Insulation Foams
Advanced insulation foams with high insulation performances allow significant energy savings and can be adapted to different building's configurations. It is estimated that these high performance foams can reduce the energy costs for heating by 30%-80%.
Insulation in Wall Cavities
Cavity wall insulation fills the space (cavity) between the two layers of the external wall of a building. As illustrated in Figure1, an existing building's wall cavity can be injected with foam as part of an energy efficiency refurbishment. In case of new construction, normally the cavity is filled up using rigid pre-foamed panels attached to the wall.
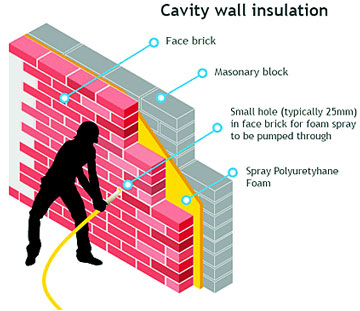 |
Fig 1 |
External Insulation
In cases where no wall cavity is present, one can opt to insulate the external walls of the building from the outside. This approach maintains the thermal storage capacity (thermal inertia) of the building external walls, thus keeping temperature fluctuations at acceptable levels. Each insulation 'stack' is composed according to the specific wall characteristics, climate and orientation of the building. Apart from the thermal insulation performance level, other material selection criteria include fire resistance, mechanical strength, stability, water absorption, permeability and cost. For most applications, the lifetime expectancy of these insulation facade systems is up to 20 years [Figure 2].
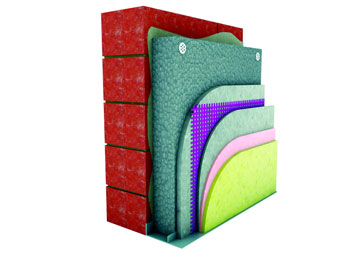 |
Fig 2 |
Internal Insulation
In case of historical facades as often found in Europe's older inner cities, buildings can also be insulated from the inside. By applying a layer of high performance insulation foam covered with for example plaster or plasterboard, this approach does not alter the external appearance of a building. Obvious disadvantages include a loss of net interior space (the thickness of the insulation layers) as well as an effect opposite to that of PCM: by insulating the interior space from the dampening effect of the stone walls, the thermal inertia of the interior is actually reduced, making the interior susceptible to stronger fluctuations under certain climate conditions.
5. Vacuum insulation panel (VIP) modules
Vacuum insulation panel (VIP) modules provide design freedom when refurbishing glass facade buildings. Their insulation performance is some three times higher than conventional insulation materials. Until recently, VIP was seldom used in buildings due to their fragility and the risk of damaging the vacuum by perforation. However recent products encapsulate the vacuum inside a double glazing package, allowing their use in glass-intensive building facades that need a strong improvement of their thermal insulation performance. VIP at the moment is still substantially more expensive than conventional insulation materials, among other reasons because they are still in the introduction phase.